- Elkem
- About Elkem
- Health, Safety and Environment
- HSE management systems
EHS management systems
Elkem has a comprehensive, internally developed corporate HSE management system called FOKUS. The programme is named after the Norwegian word for “focus,” implying the need for high attention to environment, health and safety issues throughout the organisation. FOKUS applies to all sites and activities worldwide, and all Elkem employees are covered by the system.
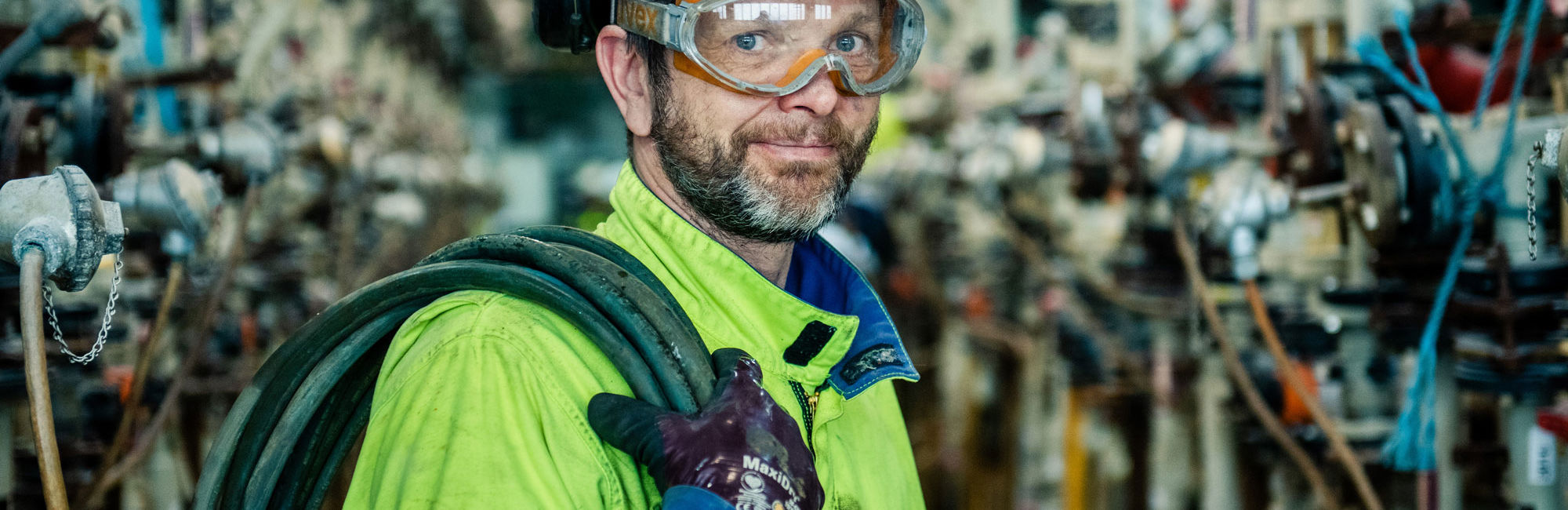
Requirements and provisions in the system are also applicable for all contractors (100%) working on Elkem property. In addition, suppliers of raw materials and goods are also required to comply with basic HSE rules and regulations as part of our contractual purchasing agreements with them.
Elkem’s HSE management system is built around recognised international standards for HSE management and covers applicable HSE topics that have been identified through extensive risk assessment at all sites. Compliance with the system is internally audited at site-level by corporate and divisional resources routinely. Elkem’s corporate Vice President for HSE is responsible for Elkem’s HSE management system.
See the overall requirements in our HSE Policy.
The 5 fundamental guiding principles of FOKUS
Principle 1: “Improvement has no limits” defines the way we work encouraging employees to question current conditions and work continuously with improvements.
Principle 2: “Zero harm philosophy” promotes the idea that all incidents and injuries can be prevented and highlights our priorities. Incident and injury prevention are just as important as production, quality, sales, delivery times, efficiency and cost control.
Principle 3: “Focus on understanding and removing causes” is about the importance of reporting, investigating and mitigating any incident that may cause harm to people or the environment.
Principle 4: “Hazard identification, risk analysis and action implementation” supports the efforts to truly understand possible negative effects of our operations and to mitigate them with effective measures.
Principle 5: “Active involvement” highlights our human capital at all levels of the organisation as the most important prerequisite for success in our EHS work
All of these principles come together and are visualised in the model we use to present and describe how we manage EHS:
Commitment
Elkem employees, and contractors working on Elkem property are expected to be fully committed to a safe and healthy workplace, and to minimise the effects of our operations on the environment.
Our commitment to HSE is stated in our General Policy.
Health, safety and environment (HSE) are always Elkem’s first priority. Elkem strives to be an environmentally conscious company, with a safe and healthy working environment. Our HSE efforts are based on a zero harm philosophy. A zero harm philosophy implies protecting the health and safety of all people working at all Elkem locations. It also means running operations with resource-efficient processes and in such a way that negative environmental impacts are minimised throughout the value chain.
We show our commitment by:
- Having clearly defined responsibilities and accepting accountability for HSE at all levels of the organisation.
- Prioritising individual health and safety when choices have to be made.
- Setting ambitions and goals and striving for continuous improvement in HSE
- Using the same HSE systems, tools and methods, and having the same expectations for HSE performance across all global operations.
Education and training
Elkem employees receive comprehensive documented HSE training to ensure full understanding of hazards in the workplace and how they can avoid harm during daily operations. Training activities include:
- Basic training in Elkem’s HSE management system FOKUS, which is mandatory for all employees.
- Specific work-related training for each work operation and each tool employees are required to use to ensure they have necessary competence to do the job safely and without harm to their health or to the external environment.
- Awareness training to ensure each employee understands how their personal behavior can affect the health and safety of themselves and others.
Training needs and completed training activities are reviewed annually through development discussions with each employee and documented at site level. Key performance indicators for training can be found under Targets and Performance.
Contractors working on Elkem property must also document their HSE training and competence to perform their work in a safe and health manner. A contractor approval process includes special Elkem-specific HSE training (link to contractor approval)
Organising
In Elkem, HSE is defined as a line-management responsibility where managers at all levels of the organisation are accountable for the HSE performance in their organisations and locations.
To ensure line-management’s ability to fulfill this responsibility each site has an appropriate HSE organisation based on the size of the organisation and the level of risk. Examples of typical functions are HSE managers, safety coordinators or technicians, environmental managers, occupational health resources, emergency response resources, etc. All HSE resources are ensured necessary competence either with formal education or in-house training dependent on area of responsibility. These functions operate as a help-chain for line-management in addition to having a control function.
In addition to hired HSE professionals, employee representatives are also elected by peers or appointed by management at each site to hold HSE roles. These roles are designed to help ensure worker involvement in EHS activities. Joint HSE committees with worker representatives are also established to discuss plans, targets and results. Meeting frequency and participation varies from site to site depending on the size of the organisation and the level of identified risk.
Communication
Open, honest and transparent communication is important for Elkem. In connection with basic HSE training, employees are introduced to different communication methods and essential approaches for good communication, both visual and oral. Communication is also followed up in self-assessments and audits with special attention to the communication climate in the organisation to ensure successful involvement and employee motivation.
Measurement
Measurement is an important enabler in Elkem’s HSE efforts and builds on the principles of Plan – Do – Check – Act.
A number of Key Performance Indicators are reported at site, divisional and corporate level. The main corporate KPIs include both leading and lagging indicators focusing on injury and deviation statistics, prevention activities and non-conformances. See Targets and Performance for main corporate KPIs.
Hazard control safety
Risk identification and assessment is the basis for all hazard control and prevention activities in Elkem and is mandatory at all levels of the organisation. Levels of risk assessment include:
- General risk assessment at site and corporate level is updated minimum annually and gives an overall picture of the main risks and mitigating measures to reduce these to an acceptable level.
- Specific risks for any facility, machine or work operation that may cause harm are mandatory before using any of these.
- Risks initiated or triggered by change (Management of change) are identified and assessed before changes are made.
Elkem’s production activities are split into two main groups; high temperature smelting/treatment and chemical processing. In addition to general personal safety issues like fall prevention, mobile equipment, machine safety, energy isolation, lifting operations and confined space entry the two main areas carry specific safety hazards tied to their key processes.
- For high temperature smelting and treatment, there are risks of explosion and fire because of high temperatures (>2000 C) and metallic or carbon dust generated in the process.
- For chemical processing there are risks of explosion and toxic emissions because of the use and generation of flammable and toxic chemicals.
All of these processes are kept in control and capable with necessary risk reducing measures, routine inspections, preventive maintenance and close follow-up to prevent harmful incidents.
Elkem has a number of corporate tools, standards and guidelines covering critical safety topics to ensure the same level of safety at all Elkem sites around the world. Based on these standards, local safety legislation, and their own risk assessments, each production unit is responsible for developing and implementing their own incident prevention programs. Compliance is followed up with corporate HSE audits.
Personal protective equipment necessary to prevent harm is available for all employees free of charge and all employees have the right to remove themselves from work situations they believe many cause harm or injury without reprisals from Elkem.
Hazard control health
Comprehensive risk assessments are the basis for identifying and mitigating health related hazards in the working environment. Main health-related risks for Elkem’s production activities include exposure to harmful dust, chemicals and substances, noise exposure, and ergonomic challenges. In addition to public regulations in these areas, Elkem also has corporate standards, guidelines and tools to ensure the same level of health protection at all Elkem sites around the world.
Employees who may be exposed to harmful exposures (dust, noise, chemicals) are subject to routine health checks including base-line health assessment when hired. Potential exposures in the working environment are routinely measured and actions implemented if exposures are over recommended levels.
Applicable sites also have access to occupational health services, either in-house services or contracted services that work together with the site to map health hazards and identify improvement measures. Employee health data is protected in accordance with national legislation and cannot be used for any favorable or unfavorable treatment of employees.
Personal protective equipment necessary to avoid harmful health exposure is available for all employees free of charge and all employees have the right to remove themselves from work situations they believe many cause harm or illness without reprisals from Elkem.
Elkem does not have corporate programs for voluntary health promotion outside of the working place but encourages sites to do this locally. Typical examples of programs initiated at site level include support to give up smoking, reduce drug and alcohol addiction, and increase healthy physical activity.
Elkem does not have a general policy for providing health insurance for employees as many countries where Elkem operates already have public systems for this. Local rules and local agreements are followed at all Elkem sites.
Incident management
Elkem has a comprehensive incident management system and expects all employees to report any injuries, incidents, unsafe conditions, deviations and non-compliances. All reports are subject to investigation, mitigation and sharing where appropriate for learning and improvement. Serious incidents are subject to comprehensive root cause analysis.
Recordable injuries and High Risk Incidents are presented for corporate management on a weekly basis for discussion. See Targets and Performance for incident statistics.
In addition to reporting, Incident management also includes emergency preparedness. All sites have emergency plans and emergency resources tailored to their level of risk. This varies from simple first-aid and fire extinguishing equipment, to fully equipped in-house emergency response teams.
Work practice controls
All identified risks are managed, either with technical controls or with administrative controls where it is not feasible to fully eliminate the risk with technical means.
Elkem’s administrative controls include a number of corporate and divisional standards covering high risk areas. They also include detailed standard operating procedures at all sites for any operation that may cause harm. Employees are closely involved in the development of these procedures and are fully trained to be able to follow them. Employees also receive refresher training routinely.
Compliance with rules and standards is followed up with visible leadership and co-workers who care about each other’s health and safety. Two of Elkem’s main HSE slogans are “Observe – React – Correct” and “Thanks for letting me know”. Both focus on employees helping and reminding each other to follow the rules and work safely.
When disciplinary actions are necessary, they follow agreements with employee representatives on fair disciplinary measures with oral or written warnings. Employment termination is the most serious form of internal disciplinary action allowed.
Audit programme
Elkem has a comprehensive Corporate HSE audit programme, where all production sites are audited on site, at minimum every other year.
The target for 2020 was 20 audits. Because of COVID-19 travel restrictions only 7 of these were done during the year. The rest will be moved to 2021 when travel restrictions are lifted.
Contact us
Take your business to the next level by partnering with a world-leading material manufacturer.