- Elkem
- Sustainability
- Policies, strategies and reporting
- Previous reports and related information
- Sustainability reporting 2019
- Elkem sustainability report 2019
Elkem sustainability report 2019
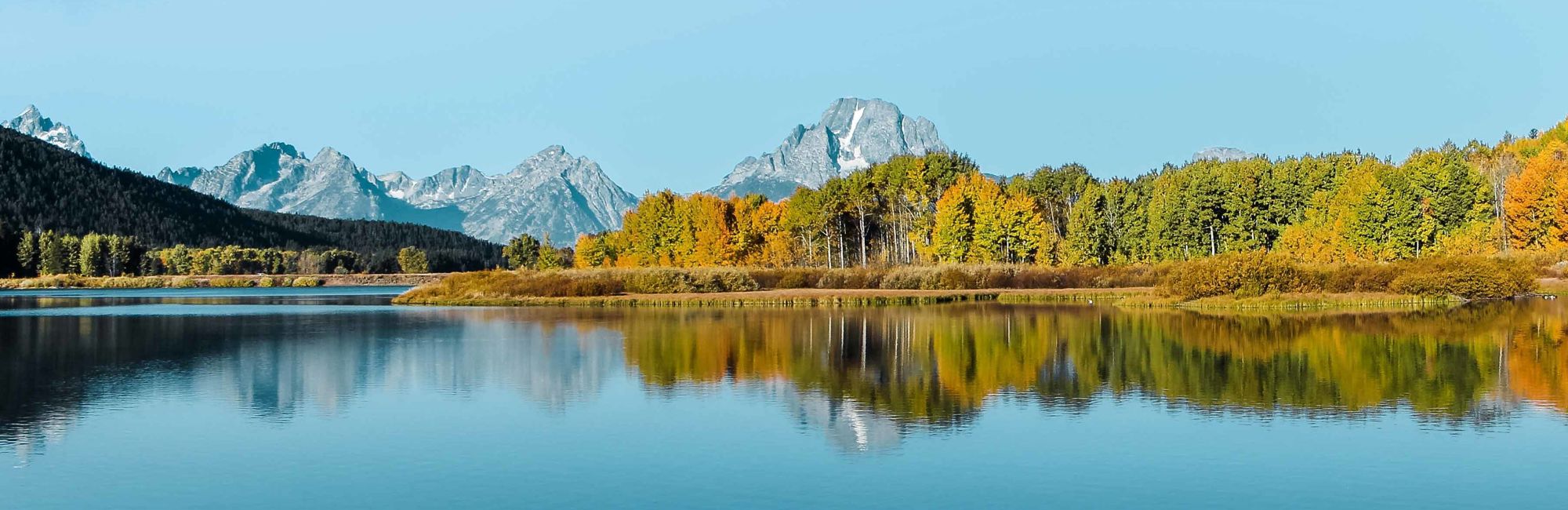
Introduction to Elkem and sustainability reporting
Who we are and what we do
Established in 1904, Elkem is one of the world's leading companies for environmentally responsible manufacturing of metals and materials.
Elkem is a fully integrated producer with operations throughout the silicon value chain from quartz to silicon and downstream silicone specialities, as well as speciality ferrosilicon alloys and carbon materials.
Elkem has 6,370 employees and consists of four business areas: Silicones, Silicon Materials, Foundry Products and Carbon. Headquartered in Oslo, the company's 29 production sites and extensive network of sales offices and agents around the world ensure proximity to customers and access to attractive end markets.
Elkem was re-listed on the Oslo Stock Exchange in March 2018. Elkem's total operating income in 2019 amounted to NOK 22,668 million, with an EBITDA of NOK 2,656 million.
Vision and values:
Elkem’s vision is “to contribute to a sustainable future by providing advanced silicon, silicones and carbon solutions, adding value to our stakeholders globally”.
Our values are Respect, Involvement, Precision, Continuous improvement.
For full financial statements for 2019, please see the annual report, here.
Sustainability in Elkem 2019
Elkem’s mission is to contribute to a sustainable future by providing advanced silicon, silicones and carbon solutions, adding value to stakeholders globally. Adding value to stakeholders means that Elkem is committed to securing sustainable economic growth with a responsible environmental footprint. Simultanously, Elkem strives to be a positive and accountable social actor within the company’s sphere of responsibility.
Elkem’s sustainability agenda is divided into four areas based on dialogue with internal and external stakeholders. These are energy and environment, societal impact, attractive employer, and compliance and governance.
In 2017, a set of sustainability targets were developed to allow stakeholders to monitor progress through annual reporting. The targets are linked to the four focus areas that are considered challenges and opportunities for Elkem. We were therefore pleased to receive a gold rating by the business sustainability rating company EcoVadis for the first time in 2019.
As an international company with a global presence, Elkem welcomes the increased focus on sustainability and supports transparency in these issues. Elkem will continue to increase efforts in order to understand and improve the organisations sustainability footprint.
Sustainable solutions for global challenges:
For Elkem, the changing landscape is an opportunity as well as a challenge. The opportunity is found in products that are critical input factors to a vast number of applications that are necessary to meet the increased demands for renewable energy, energy storage, mobility solutions, infrastructure improvements, digitalisation and health care.
Ferro-alloys, silicon and silicones present a clear opportunity for Elkem and the demand is expected to increase in parallel to the expected demand growth for low-carbon technologies.
The challenges are found in current technologies for producing the same critical raw materials that are necessary to build wind turbines, solar panels, batteries, electric vehicles and other environmentally friendly applications. The current production technology is both energy intensive and emits CO₂. Elkem is committed to reducing energy consumption and C02 emissions as far as technically feasible with current technology, in addition to developing new technology that will make production carbon neutral.
Stakeholder engagement
Elkem’s operations have significant impact on societies through the value chain. Many of Elkem’s plants are cornerstone employers and important contributors in local communities, securing safe jobs and infrastructure, paying taxes and supporting local community development. As a long-term partner, Elkem values open dialogue with all of its stakeholders including local communities, governments and other partners such as research institutions, customerscustomers and suppliers. Respect is one of Elkem's core values. Our stakeholder dialogue is based on respect for individuals, society and the environment. Maintaining contact with the various stakeholders helps Elkem understand the role we play in local communities and society as a whole, as well as building long term, mutual trust.
In 2019, we continued to develop our stakeholder management tool to ensure that each location has a structured way of securing stakeholder engagement. Implementation of the tool is planned for 2020. For more information about our stakeholder dialogue and community work, please visit the societal impact chapter on page 80.
Elkem's stakeholders:
- Employees
- Customers and suppliers
- Local and national authorities
- Corporate management team
- Local communities and organisations
- Investors and shareholders
- Unions
Materiality assessment
To ensure compliance with Global Reporting Initiative (GRI) and the new stakeholder landscape arising from Elkem´s re-listing on the stock exchange, the group carried out a more extensive engagement process with stakeholders last year. The materiality assessment table on the next page highlights Elkem´s priority issues on sustainability based on comprehensive dialogue with both internal and external stakeholders.
The material topics with highest priority in our materiality assesment can be found at the top right of the table. These topics are covered in our report.
Policies and reporting
Elkem’s management of Corporate Social Responsibility and sustainability is defined in the following policies:
- Corporate governance policy of Elkem ASA
- Elkem policy for corporate social responsibility
- Mandate for the CSR steering committee
- Code of conduct
- Speak up policy
- Anti-corruption policy
- Competition law compliance policy
- Elkem Code of Conduct for business partners
The corporate governance policy for Elkem ASA is approved by the Board of directors and provides the overall strategic approach while the other procedures are approved by corporate management. A dedicated steering committee for CSR is responsible for initiating and following up corporate CSR efforts.
Elkem’s sustainability report is the main channel for CSR reporting and has been prepared in accordance with the GRI Standards: Core option and complies with the requirements set out in the Oslo Stock Exchange guidance on the reporting of corporate responsibility.
For investor relations purposes, we have also prepared an index listing key ESG topics for Elkem (with referrals to corresponding ESG reporting). The index is found on www.elkem.com.
The sustainability targets developed in 2017 will be reported on for the second time this year. You find the targets and progress in each chapter of the report.
Targets for reporting
The targets below reflect how Elkem overall manages engagement and reporting on sustainability. Each chapter in this report includes specific targets, aligned to our material sustainability topics.
Commitments
Elkem is committed to conducting business in support of the United Nations Sustainable Development Goals (SDGs) and the Paris Agreement ambitions. As a member of the United Nations Global Compact, Elkem ensure that our business is aligned with the ten UN Global Compact principles. Elkem is committed to following the United Nations Guiding Principles on Business and Human Rights and have made available an updated UK Modern Slavery Act statement.
Elkem adheres to the principles of “the Norwegian Code of Practice for Corporate Governance” issued by the Norwegian Corporate Governance Board (“NUES” or the “Code”). The objective of this Code is that companies listed on regulated markets in Norway will practice corporate governance that regulates the division of roles between shareholders, the board of directors and executive management more comprehensively than is required by legislation.
Elkem’s silicones division is a member of the Responsible Care Global Charter, the chemical industry’s global initiative to drive continuous improvement in environment, health, safety and security performance. Membership entails a commitment to managing chemicals safely throughout their life cycle. For more information, please visit the societal impact chapter on page 80.
Elkem is committed to complying with international regulatory requirements and provides safety data sheets (SDS) for all its products in accordance with the UN Globally Harmonized System of Classification and Labelling of Chemicals (GHS) or its national implementations.
Energy and environment
Targets and KPIs
Using highly developed production technology, Elkem converts natural resources into products that today's society is fully dependent on. This demands a lot of energy and affects the environment – directly and indirectly.
The process of converting quartz to silicon is a high temperature smelting process that consumes vast amounts of energy. Even though the energy base for most of Elkem's production is renewable, it has an environmental effect. The production process itself uses carbon sources like fossil coal, charcoal and wood chips as a reductant in the chemical conversion giving emissions of CO₂, NOₓ and SO₂. These emissions are inherent to the process and cannot be fully removed with today’s technology. In Elkem's downstream business, there are also potential environmental impacts to air and water when converting silicon to silicones.
All of these environmental impacts are identified and documented with measurements or calculations showing performance compared to permits given by government authorities where Elkem operates, and/or improvement targets set by Elkem. Key environmental parameters are reported quarterly at corporate level. In addition to this, environmental deviations are reported, investigated and closely followed up in a timely manner. In 2019 there were no serious environmental incidents.
Because of the potential environmental impacts, all applicable Elkem sites are required to have an appropriate Environmental Management System and many are also ISO14001 certified. In addition, applicable sites are required to have Energy Management Systems and some are also ISO50001 certified (see certification list here).
ENVIRONMENTAL STRATEGY
In 2018, Elkem renewed its environmental strategy confirming its commitment to:
- Full compliance with all applicable environmental regulations wherever Elkem operates worldwide.
- Creating and sustaining a strong environmental reputation wherever Elkem operate worldwide.
- Ensuring sustainable production and emissions/discharge control based on our knowledge of the environmental effects of our production. This also applies in countries where applicable environmental regulation is weak or non-existent.
- Strengthening our position in the development of technology and materials that enable reduction in greenhouse gas emissions throughout the world.
The strategy introduced a comprehensive set of KPIs with quarterly reporting on energy consumption, emissions to air and water and waste/process-products. It is also followed up at production sites with detailed road maps showing how targets can be met. The main environmental KPIs are:
Energy: Consumption, recovery and efficiency
ENERGY: CONSUMPTION, RECOVERY AND EFFICIENCY
Energy is of upmost importance to secure necessary supply while at the same time reducing Elkem's global greenhouse gas footprint. A new regulatory framework, such as concessions, directives, taxes and positive stimuli in the form of public support substantiates the importance of increased focus on energy efficiency.
Parts of Elkem’s value chain are highly energy intensive, with silicon, ferrosilicon and foundry alloys being produced in electric arc furnaces. Elkem’s smelting furnaces consume just under 5 TWh of electrical energy per year.
Elkem was an industrial pioneer in the utilisation of waste heat, with the first energy recovery system on a smelting furnace being installed already in the 1970s. Recovered heat from smelting furnaces can be utilised as hot water for district heating, steam for other production processes and to generate new electricity. Electricity is sold back to the grid while hot water and steam are used both internally and externally to supply other companies and communities in the vicinity of each plant.
Energy consumption:
Total gross electricity consumption in Elkem in 2019 was 6,010 GWh, down from 6,228 GWh in 2018. Most of this change is related to reduced production because of the general global market situation for Elkem’s main products. More than 83% of the total gross electricity consumption is based on renewable power production. With the exception of one smelter in China, all smelting furnaces in Elkem run on renewable electrical energy. In addition to electrical energy, Elkem also consumes approximately 1.4 TWh of other types of energy for internal vehicle operation and heating/cooling of facilities and processes. Most of this is fossil based energy.
Energy recovery:
Elkem has a long-term strategy to increase energy recovery year on year as part of its climate programme. A number of Elkem’s production processes generate surplus heat that traditionally has been emitted through off-gas systems or cooling systems. Much of this can be recovered to hot water for district heating, both internally on site and to other public facilities and industries close to the plants, and to steam used in industrial processes and/or to generate electricity.
The potential for energy recovery has been mapped at all smelters. Three of Elkem’s smelters already have large boilers attached to their off-gas systems to recover substantial amounts of energy to steam or electricity. A fourth facility will come online in 2020 giving another 270 GWh of electrical energy. Globally, a total of 698 GWh heat and electricity was recovered from our plants in 2019. This represents an increase of 54 GWh from 2018.
Energy efficiency:
All Elkem sites are required to have an appropriate energy management system and an energy inventory showing the potential to increase energy efficiency and thereby save energy. Examples of this could be replacing old, inefficient electrical motors with new motors with advanced digital energy control. For examples, please visit www.elkem.com.
In 2019, Elkem realised energy reduction efforts of 51 GWh in projects related to infrastructure and utility consumption, of which several initiatives received public support.
C02 emissions, trading schemes and other emissions to air
CO₂ EMISSIONS AND TRADING SCHEMES
Elkem emitted a total of 2.15 million tonnes of CO₂ from fossil carbon in 2019, down from 2.54 million tonnes in 2018. This is mainly because of lower production, but also because of increased use of bio-carbon in the smelting process. About 81% of direct CO₂ emissions are generated in the smelting furnace reduction process where carbon (C) reacts with oxygen in quartz to produce silicon/ferrosilicon. As we are not able to measure this type of emission directly, they are calculated based on third party certificates of carbon content (TC) in raw materials. Numbers for CO₂ from other sources, including heating and fuel, are based on standard conversion factors in accordance with EU/ ETS Guidelines.
As CO₂ emission is inherent to the smelting process with current technology, total emissions will vary year on year based on market conditions and capacity utalisation. As CO₂ is inherent to the smelting process with current technology, total emissions will vary year on year based on market conditions and capacity utilisation. During the past few years Elkem has seen an increase in the group's total CO₂ emissions. All of this can be related directly to production expansion. From 2017 Elkem has increased production with five smelting furnaces; two in Norway, four in China and one in Paraguay. The furnace in Paraguay runs solely on hydroelectric power and uses only bio-carbon as a reductant, making its operations close to carbon neutral. The increase in CO₂ is also connected to the acquisition of upstream silicone activities in China, which uses a coal fired boiler to produce steam used in the production process.
Elkem has a number of ongoing activities to reduce its CO₂ footprint. These activities are basically grouped in three main areas; Increasing material and energy efficiency, replacing fossil carbon with bio-carbon and developing new carbon neutral smelting technology.Examples of progress in all these areas are detailed on www.elkem.com.
One of Elkem's main CO₂ reduction strategies is replacing fossil carbon with bio-carbon in our smelting operations. The goal is to reduce the fossil carbon footprint at our Norwegian smelters with 20% by 2021, and by 40% by 2030. In 2019 the group had already met the 2021 goal and continues to work closely with partners to develop efficient and more environmentally friendly production of bio-carbon for silicon and ferrosilicon production.
Trading schemes:
Most of Elkem's smelters are subjects to the EU/ETS system and its external revision schemes (plants in Norway and Iceland). From the start in 2013, Elkem was granted on average 1.2 million free allowances per year as part of the EU system to avoid carbon leakage where production would be moved out of Europe to other countries without carbon trading schemes. When it was identified that smelters in Norway had been allocated fewer free quotas than other countries in Europe, the allocation was successfully appealed increasing the number of free quotas allocated to Elkem’s Norwegian smelters.
OTHER EMISSIONS TO AIR
Elkem emits both NOₓ, SO₂, and dust. These emissions are mainly from the carbon calcining process, the silicon/ferrosilicon smelting process and the upstream silicone-based product process. Major emission variations are tied to changes in production volume, but can also be affected by the quality of raw materials, process control and investment in filter systems.
NOₓ:
Elkem continues its efforts to reduce emissions of NOₓ through equipment design and process control. Numbers for 2019 show a reduction of approximately 5% from 7,070 tonnes in 2018 to 6,718 in 2019.
SO₂:
In 2019 Elkem emitted 7,309 tonnes SO₂, down from 9,000 tonnes in 2018. Most of the reduction is based on reduced production because of global market conditions for Elkem’s main products. For SO₂ the main focus has traditionally been on sourcing raw materials with a lower Sulphur content. As this potential is limited, scrubbing systems are also being considered where this is feasible. In 2018, Elkem Carbon Norway finished the installation of a large SO₂ filter with support from the Norwegian SO₂ fund. Unfortunately, the installation has not operated as expected due to technical issues and has therefore been out of operation for most of 2019. Most of the technical issues have now been solved, but there still are challenges attaining the full effect of this major investment. Elkem Bjølvefossen is also evaluating a similar project.
Dust:
Elkem allocates significant resources to combat dust. However, extremely high temperatures and ultrafine particles that disperse very quickly make it especially difficult to capture dust generated in some of the production processes.
Water and waste management
WATER MANAGEMENT
Historically, the majority of Elkem’s production facilities were located in areas where freshwater supplies were abundant and more than sufficient for Elkem’s production activities without any water stress issues. Water management activities were mainly focused on discharge control to ensure that public permits are respected, and that water bodies close to our production sites were duly protected against harmful discharge. As Elkem has expanded globally and migrated more into chemical processing, water economisation, recovery and reuse on site have become more important parts of the water management programmes.
Water is an important raw material in the production of base and intermediate silicones and is also used extensively in the different processing steps. The fact that Elkem’s upstream silicones production is located close to important freshwater bodies in both France and China, where effluent from chemical production is closely regulated, has also increased the focus on water management.
Water body monitoring (both fresh and saltwater bodies) has been done at Elkem’s plants for decades in accordance with applicable regulations and permits. In Europe this means compliance with the EU Water Framework Directive, while other regulations apply in other regions around the world where we operate. There are three main groups of pollutants from Elkem’s production that can have a negative effect on water bodies close to production sites;
- Heavy metals found naturally in raw materials used in the production of silicon, ferrosilicon and carbon products can be released during the production process and emitted to air. Rain and water run-off will enable these to find their way to water bodies.
- Polycyclic aromatic hydrocarbons (PAH) components found in raw materials used in carbon products are harmful for aquatic life. These find their way to water bodies either through direct discharge of process water, or by wash-off of particles emitted to air and end up in marine life and sediments. Potential and real effects are closely followed up at applicable plants.
- Organic substances that reduce the oxygen content in water bodies, so called chemical oxygen depletion (COD) substances are the main challenge in the production of silicones. This is especially critical for the two upstream plants located in China and France that produce upstream silicones.
In addition to discharge from current production there is a potential from the ground on and around production sites. A number of Elkem’s older plants are situated where industrial production has existed for more than a century. Through the years, facilities were built on landfills and/or had their own landfills as this was permitted at that time in history.
All of these, both historical and current discharges are closely followed up and effective water treatment plants are used where necessary to reduce the effect to an acceptable level. Remediation efforts are also implemented and/or planned where needed.
The total freshwater consumption in Elkem was approximately 80 mil m3 in 2019. Most of this consumption is in areas with abundant freshwater supplies and no signs of water stress. Approximately 10%, is however, located in areas where the availability of fresh water is a concern like South Africa and parts of China.
WASTE MANAGEMENT
Elkem operates with a zero-waste philosophy closely tied to our business system (EBS). This includes a strong commitment to reduce the generation of waste at its source, to recycle or regenerate byproducts to the extent this is feasible on site, and to separate any remaining waste before delivery to external waste management to enable recycling.
Historically, waste from Elkem's smelting activities consisted mainly of non-hazardous inorganic materials such as slag, product fines, quartz fines and a smaller quantity of organic fines from wood-chips and charcoal. For all of these, extensive projects have been initiated to re-cycle and re-use instead of depositing in landfills. Many of these have been very successful by both creating new products and by better utilisation of raw materials (see www.elkem.com).
With silicones there is much higher content of organic waste and hazardous waste from the different production processes. Destruction of hazardous waste is managed by certified external suppliers, while other waste will either be incinerated or landfilled in accordance with local regulations. Many projects have also been initiated to reduce waste at its source and to regenerate chemicals for re-use instead of destroying or depositing them.
Waste to landfill in 2019 was 340,000 tonnes including 3,500 tones hazardous waste managed by certified third party service suppliers. Recovery of biproducts and consumables that could be used in own production or sold to others constituted 67,000 tonnes. In addition, 136,000 tonnes of recovered smelting furnace dust was processed to Microsilica which is a full value product with many uses including concrete strengthening for the construction and building industry.
ENVIRONMENTAL DEVIATIONS
There were no significant spills, defined as those that have a lasting environmental impact, or significant environmental incidents in 2019. A total of 66 environmental deviations were reported globally in Elkem for 2019. Most of these were small brief permit deviations from Elkem’s upstream and intermediate silicone production in France and China.
Because of its location close to one of China’s largest freshwater bodies, Elkem Xinghuo is subject to very strict requirements for discharge to water and has been under close follow-up from the authorities during 2019 as water treatment facilities were not sufficient to meet these requirements. Production reduction has been necessary in 2019 to meet the requirements.
Product stewardship, substances of concern and conflict materials
PRODUCT STEWARDSHIP, SUBSTANCES OF CONCERN AND CONFLICT MATERIALS
Product stewardship focuses on the environmental, health and safety effects of Elkem’s products through storage, transportation and use by the group's customers. It includes fully understanding potential hazards with our products and giving clear information on safe use and handling through safety data sheets and other information to customers and partners.
Elkem has a high focus on product stewardship with resources at both corporate, divisional and plant level.
Substances of very high concern (SVHC) in Elkem’s products:
Elkem has three main product areas where substances of concern occur:
- For silicon products and ferroalloys, heavy metals are naturally occurring elements in raw materials.
- For carbon products, coal tar pitch high temperature is used as an intermediate in the production process.
- For silicones, D4 and D5 are generated as intermediates in the production process and used to produce downstream silicone products. In addition, some additives used in the production process are listed as SVHC in Europe.
Silicon products and ferroalloys:
For the production of Elkem’s silicon products and ferroalloys, natural raw materials are carefully selected in order to meet the product specifications. Natural raw materials, as well as the final products, may contain trace amounts of “elements of concern”, i.e. heavy metals. However, the concentration of such elemental impurities is as low as a few ppm (parts per million) and thus, far below the generic threshold value of 0.1% that would trigger regulatory action. No SVHC’s currently listed on REACH annex XIV, are intentionally added to Elkem’s silicon and ferroalloy products. A number of leaching tests have been carried out on Elkem’s products in order to assess bioavailability of elements of concern. Leaching of critical elements is so low that the products would comply with European regulations for the use in toys (EN 71-3, safety of toys) or in electronic equipment (RoHS directive), and even meet the recommendations of the Federal Institute for Risk Assessment Germany for fillers in polymers with food contact (BfR LII).
Carbon products:
Elkem Carbon is one of the world’s largest manufacturer of Søderberg electrode paste that is used in metal production around the globe. Historically, Søderberg electrode paste has been made of coal tar pitch and coke. The use of coal tar pitch, high temperature, requires authorisation under the European REACH regulation. However, since the use of coal tar pitch in Søderberg electrodes is considered as intermediate, it is exempted from authorisation. Elkem Carbon has been working successfully on the replacement of hazardous pitch with green substitutes and can now offer an increasing range of products free of polycyclic, aromatic hydrocarbons (PAH). This is an important step towards a non-toxic workplace environment, for both Elkem and customers.
Silicones:
D4, D5 and D6 are key intermediates for all silicones products. There has been extensive research and discussion the past years to identify and verify possible hazards with these products, but environmental authorities around the world have still not come to a common understanding of the possible environmental effects. As final environmental classification in Europe is still ongoing, Elkem continues to take all necessary steps to reduce any environmental risk (see www.elkem.com for more information on D4, D5 and D6).
For some downstream products certain acids and catalysts defined as SVHC are currently in use for the formulation of some products. These are kept under close control and substituted whenever possible. As they are only part of the production process, they do not cause any hazard in the final product.
Conflict materials:
Conflict minerals refers to raw materials or minerals that come from a particular part of the world where conflict is occurring and affects the mining and trading of those materials. These conflict minerals are tin, tantalum, tungsten (the “3T’s”) and gold. Elkem uses chemical compounds made from some of these in small quantities in the silicones production process and has strict sourcing controls to ensure that procurement of these are done in full compliance with applicable European regulations.
Safe transportation of hazardous goods:
Potential hazards in connection with the transportation, handling and storage of all of Elkem’s raw materials and products are fully analysed, and measures to ensure this can be done safely are documented and made available to logistics supplier and customers. The main risks include loss of containment leading to the possibility of fire or toxic release from raw materials and products under transportation. Logistics suppliers that handle hazardous goods for Elkem are closely screened and required to have all applicable certifications for vehicles and drivers. In Europe there is also close cooperation between different chemical producers with agreements to give assistance to each other in case of emergency situations with the transportation of hazardous goods.
Attractive employer
Targets
Elkem's skilled and dedicated employees are the basis for success and Elkem strives to remain an attractive employer, both to retain existing employees, and to attract new ones. Key priorities in these efforts are ensuring a safe and healthy working environment, facilitating training and competence building, as well as promoting equality and diversity.
Environment, health and safety (EHS) are part of the foundation of the company and is always our first priority. EHS efforts are based on a zero-harm philosophy. The safety of our employees is paramount. Elkem strongly believe, and have shown at many plants, that our production can be conducted without any harm to our employees. Elkem takes responsibility for all activities on Elkem property and is committed to ensuring that employees and contractors working at Elkem sites can do so without harm.
Supported by a strong company culture, Elkem continuously work to be a safe and attractive employer for current and future employees. Organisational development, continuous talent management and systematic competence development are key to ensure the successful growth of the company.
Common culture: Elkem Business System
Elkem has more than 6,370 employees working at 29 production sites and a wide range of sales and administration offices spread around the world.
As in all organisations, Elkem evolves and develops over time and the company culture evolves with it. Elkem’s values are involvement, respect, precision and continuous improvement. Along with the Elkem Business System (EBS), these are at the core of Elkem’s company culture. EBS is Elkem's business and leadership philosophy and also a toolbox that enables a common language and working methods for all employees to achieve both personal and business success. EBS covers all areas of work, including productivity, quality and cost efficiency. At the heart of EBS, is a dedication for involving our people in improvement work and empowering them to solve problems. Training and competence development at all levels of the organisation is a central part of the philosophy.
Elkem has considerable expertise in understanding and controlling processes which generally trend toward instability. During the 90's, bringing our processes into stable and predictable operation was a cornerstone of the company's profitability. Today, Elkem's processes are better understood and optimised, but the focus on Elkem's people is as important as ever. Only people can identify and solve problems. In doing so, they will gain valuable experience, knowledge and personal development. That's why Elkem in 2019 decided to move empowered people to the centre of the EBS Logo. Everything starts and ends with our people.
EBS assessments to promote involvement and continuous improvement
- All sites are assessed by a corporate EBS team bi-yearly to measure involvement and improvements, and to encourage further development. In addition, all business units are encouraged to perform self-assessments yearly.
- Topics in the assessment include learning and competence development and structure / formalisation of improvement work at all levels. Units are expected to show current mapping of knowledge and skills in their work force, and a plan for closing any competence gaps as well as for further development of their employees.
- Focus from the corporate team is on involvement, knowledge and information sharing, and on management commitment to empowering their employees in continuous improvement work through shared goals and tools.
Diversity and equality
DIVERSITY AND EQUALITY
Elkem is an international company with a presence in many countries around the world. Having employees that match this global presence, representing diverse cultural and individual backgrounds, is necessary for the company to succeed. Elkem is a local employer and values the strength of local management and staff wherever Elkem is present.
Elkem is committed to ensuring equal opportunities for all our employees and an inclusive work culture. We appreciate and recognise that every individual is unique and valuable and should be respected for his or her individual abilities. We do not accept any form of harassment or discrimination based on gender, religion, race, national or ethnic origin, cultural background, social group, disability, sexual orientation, marital status, age or political opinion.
Our focus on equality and diversity, our corporate values and our code of conduct are essential topics in the Elkem Onboarding Programme (EOP), which is part of the mandatory training for all new employees. All managers in Elkem are expected to be strong ambassadors of diversity and equality, and diversity has been a key topic in the Elkem Leadership programme for several years. Elkem's new leadership development programme for first line managers worldwide also includes training on diversity. Each manager is responsible for following up the principle of non-discrimination.
Due to Elkem’s growth in the Asian region over the recent years, several initiatives have been implemented to ensure applicable training in our code of conduct and the principle of non-discrimination in this region. The Asian branch of our compliance department has adapted the corporate code of conduct training with content and ethical dilemmas based on a local business context. Training sessions have been conducted in order to ensure that all employees fully understand and commit to the code of conduct.
In order to further strengthen an inclusive and diverse work culture globally, Elkem launched a pilot project on diversity and inclusion in 2018. In 2019, several workshops were conducted in three Asian countries where Elkem is present. Key activities in these workshops included addressing different forms of discrimination, training in the Elkem code of conduct and increasing awareness among employees by discussing possible ethical dilemmas in our workday. The workshops will be continued as diversity and inclusion training for selected target groups in 2020.
Putting the spotlight on Elkem as an attractive employer for candidates with diverse backgrounds, comprehensive work was done in 2019 to review existing practices. This work resulted in several specific measures, such as implementation of mandatory diversity awareness training for recruiting managers, showcasing role models to display the diversity in the organisation, and revision of templates for job advertisements and related communications materials.
Incidents in 2019:
There was one incident reported to corporate level in 2019 regarding diversity and equality, which was handled according to company procedures. The incident was partly due to cultural differences and was managed through coaching and training of the involved parties.
FEMALE SHARE
Elkem values gender diversity and aims to achieve a better gender balance year on year.
The process industry is generally male dominated. Women are, however, increasingly expressing an interest in working in our industry as increased automation leads to less heavy manual work. A high focus on environment, health and safety ensures a better working environment and more sustainable operations.
The female share in Elkem was 25% in 2019, and Asia was the region with the highest proportion of female employees, with 28%. The substantial increase in female share from 2017 to 2018 was due to the integration of the Chinese plants Elkem Xinghuo Silicones and Elkem Yongdeng Silicon Materials, with a higher proportion of female employees.
In 2019, 24% of the leaders in Elkem were female. One concrete action to improve our share of female leaders is to actively encourage women to apply for management positions internally. Elkem strives to have at least 50% women among the participants invited to Elkem’s leadership training programmes. The female participation rate in the programme increased from 25% in 2018 to 32% in 2019.
The female share in Elkem has been stable over the past years. It has been decided to intensify the focus on attracting and retaining more women, especially in management positions. We have launched several initiatives specifically aimed at our female employees. A mentor programme targeting female mentees was established as a pilot in 2019 and will be conducted throughout 2020. The programme will be evaluated and considered for global application after the pilot period. The corporate recruitment policy and related training materials have been updated to include topics such as including female recruiters and/or managers in each recruitment process and tracking the proportion of female candidates throughout the process.
BOARD OF DIRECTORS AND MANAGEMENT
Elkem’s board of directors consists of 11 members from Germany, France, China and Norway. The female share of the board is 36%. Two of the eleven board members are in the age group 30–50 years old. The rest of the members are 51 years or older.
The corporate management team of Elkem consists of ten people from France, Norway, China and Canada. The management team consists of nine men and one woman. One of the members is in the age group of 30 to 50 years old and the rest are 51 years or older.
In 2018, Elkem started mapping the female share of man management teams in our divisions and corporate functions to get a better overview and start tracking developments. The mapping continued in 2019, excluding internal boards. The mapping showed that the female share in management teams reporting to top management in Elkem is 23%, which is the same number as 2018. Furthermore, the mapping showed great differences within the organisation. Some places in the organisation, women accounted for over 50% of plant management where in other locations, there were no women in management at all.
In 2019, Elkem started tracking the age distribution of employees. The tracking indicates that almost two thirds of the employees are 30-50 years. The age distribution for blue-collar and white-collar employees is very similar to the overall age distribution for employees.
Development and training
Elkem is active in many demanding markets and the need for continuous development and improvement is constant. The organisation’s improvement work needs to be targeted, fast-paced and of high quality. Elkem actively uses employees’ day-to-day work situation as the primary arena for learning. We believe that the best way to develop new skills is to participate in actual improvement processes and problem-solving cases based on the EBS principles. We also consider taking on new responsibilities as a very important way of learning and developing. In order to strengthen our learning-by-doing approach we also offer several in-house training programmes.
Agreeing on an individual development plan is part of the annual development discussion that all employees in Elkem shall have with their leader. Elkem’s global target is that 100% of employees of all positions and locations shall have an annual development discussion with their leader.
In 2019, 65% of Elkem employees had an annual development discussion. This is a substantial increase from 2018, when 59% of employees had such discussions. Overall, 76% of all reporting Elkem units achieved 90% or higher implementation rate. 65% of our locations met our 100% target in 2019. In 2020, we will increase our efforts and strive towards our goal of 100% in the whole organisation.
Turnover
Turnover rate is an indication of attractiveness and how well Elkem manages to retain our employees. Total turnover rate in the Elkem group was 8% in 2019. The female share of new hires was overall 30% and the female share of leavers was 17%. These numbers indicate a positive effect of our efforts to attract and retain female employees.
Collective bargaining, contractors, child and forced labour
Elkem fully endorses employees’ freedom of association and collective bargaining rights. These rights give employees the ability to create changes and find solutions with their employer and have a long tradition and strong standing in some of the countries where we operate, like Norway and France. Elkem is also present in regions where collective bargaining agreements and freedom of association is less prevalent. Our corporate CSR policy clearly states that all employees should receive information about the ability to organise and collectively bargain with management, to the extent that it is legally possible. This topic is of high importance to Elkem.
Elkem complies with local statutory requirements regarding freedom of association in all countries where we are present. Pursuant to the provisions of the Norwegian Companies Act, employees have three representatives and two observers on the board of Elkem ASA.
The level of organisation varies from country to country. In some countries the operators are organised under one collective bargaining agreement. In other countries there are no unions represented in Elkem’s entities. Elkem supports the right to exercise freedom of association and collective bargaining and in general cooperates well with the unions. This also includes our suppliers’ employees, where information about these rights are found in contractual agreements.
In 2019, Elkem started tracking the number of employees covered by collective bargaining agreements/union agreements. In total, 61% of our employees are covered by such agreements, but there are significant local and regional variations.
Child and forced labour
Elkem has operations in several countries where there is a risk of child labour and forced labour, such as Asia, South America and Africa. We take this risk most seriously, and we will not tolerate the use of child or forced labour in any of our operations and facilities. We expect the suppliers and contractors with whom we do business to uphold the same standards.
Elkem adheres to the UN Guiding Principles on Business and Human Rights, and commits to the UK Modern Slavery Act. We have a clear CSR policy to secure the rights of our employees, as well as a Code of Conduct for Elkem’s Business Partners as part of all new contracts to ensure the compliance of our suppliers.
Working at some supplier production sites or at some of our own plants is considered high risk work and must only be done by trained and qualified people.
The age limit for working in Elkem is 18 years, with exception for vacation substitutes and vocational students, where the limit is 16 years. Vacation substitutes and vocational students are only allowed to do light and simple work that is deemed safe and does not conflict with school participation.
To ensure compliance with these procedures and our CSR policy, several measures are in place. Elkem has strict routines to ensure that all official permits and registrations are in accordance with local law, and that all employees have written employment contracts, insurance coverage, correct tax payments, etc. EHS and CSR audits are regularly conducted in all plants, with specific focus on these topics for plants in high risk areas. CSR workshops are also conducted to provide knowledge and training and ensure awareness of these issues.
Elkem’s suppliers have contractual obligations to ensure that no children under the age of 15 (14 in some selected countries) work at our suppliers’ plants and that they limit hazardous work and night work to persons over 18 years of age. These standards are secured by pre-audit for approval of new suppliers and regular audits for existing suppliers, legally by contract.
Incidents in 2019:
There were no reports of child or forced labour in Elkem or with our suppliers in 2019.
Contractors
Contractors provide services of many kinds at Elkem’s plants and other locations around the world and are subject to the same EHS requirements as our own employees. All contractors receive full training and follow-up to ensure that they work in a safe and healthy environment.
The number of contract employees in Elkem was 882 in 2019, defined as non-Elkem employees working full-time for more than three months as a substitute for hired employees.
Societal impact
Targets
Elkem believes that sustainability is a core responsibility as well as a prerequisite in order to be at the forefront of our industry and to remain competitive in the future. Apart from our own operations, Elkem also has a significant social, environmental and economical footprint through procurement of raw materials, capital goods and services. The process industry plays a major role in the transition to a low carbon society and in mitigating the climate change effects.
Possibilities and challenges inherent in moving towards a more sustainable world is part of Elkem’s company risk assessments, divided into relevant areas such as market risk, EHS risk, CSR risk and financial risk. For more information about sustainability risks, please visit the introduction chapter.
Global megatrends affect our business strategy and drive Elkem’s growth, requiring that we specialise our operations and focus our products and solutions on future needs. Six megatrends have been identified as strategically important to Elkem, driving the demand for our products: Sustainability, energy demand growth, rapid urbanisation, increased standard of living, ageing and growing population, and digitalisation.
Sustainability impact of Elkem’s products
For many years, Elkem has been in close dialogue with several customers when it comes to sustainability. Through initiatives like the sustainability rating company EcoVadis’ CSR rating, we have been able to track our performance on sustainability and expectations from our customers. 2019 has been a milestone in many other ways, as our customers have notably increased their demands for information on the actual environmental impact of our products.
Elkem supports this development and works closely with customers on product life cycle analysis (LCA). We work continuously to improve the environmental footprint of our products; footprints from both CO₂ and other emissions such as NOₓ, SO₂, dust and PAH. For more information on these topics, please visit the chapter on energy and environment on page 62.
Elkem is also focusing on improving calculation and tracking of emissions. Elkem has a zero-harm vision and strives to be able to offer customers sustainable solutions. Preparing our product portfolio today will give us a competitive advantage going forward, as we expect to see an increased demand for LCA information and environmentally friendly products.
Most of Elkem's CO₂ emissions occur in the silicon and ferrosilicon processes. Our products, however, are mainly based on electricity from hydropower and are therefore characterised by lower environmental footprints than many competitor products. On average, our silicon has one third of the world average emissions calculation, which is 12 kilogram CO₂ per kilogram produced of silicon.
Also, when calculating cradle-to-grave greenhouse gas emissions of silicones, the production of silicon materials is the most relevant contribution, as it accounts for 66% of total emissions for silicones products.
The regional origin of silicon materials therefore plays a significant factor for the CO₂ emissions of silicone, because of the variation of electricity production in the different regions. Here, Elkem’s electricity mix will be a green comparative advantage when calculating LCAs.
Elkem provides products to the automotive industry. The big automotive companies have strategies to evaluate and integrate LCA in their development processes of cars, which impacts our deliveries. Elkem Silicon Materials is working on evaluating and improving the CO₂ footprint of our products and will continue to be an environmentally friendly provider of products to the automotive industry in the future.
There are CO₂ emission abatement effects from the use of silicone products, reducing the end-life effect of silicones versus competing materials. Silicone products enable more efficient transport, contribute to lighter vehicles, reduce the need for heating energy and electricity consumption and help increase efficiency. The features of silicones contribute to extend material lifetime, ensure more efficient use of materials, and can also replace oil-based plastic products, lowering the carbon footprint in material production and recovery. A study published by CES (Silicones Europe) in 2018 showed that the largest net-benefit of using silicones was found in automotive, construction and solar energy applications, and that compared to alternatives it is estimated that a net 48 kilogram of CO₂ equivalents abatement per kilogram of silicones applied.
Product stewardship in Elkem
Elkem works to ensure safe handling, use and disposal of our products. Product stewardship is defined as responsible and proactive management of health, safety and environmental aspects of a product throughout its lifecycle.
Elkem is committed to comply with international regulatory requirements and provides safety data sheets (SDS) for all products in accordance with UN Globally Harmonized System of Classification and Labelling of Chemicals (GHS). In all markets where Elkem’s products are promoted, the products must meet specific requirements and comply with certain technical, regulatory, health and environmental standards.
This is especially important for our silicones division. Proactive chemical management and protection of the environment and human health are fundamental prerequisites for conducting our business and securing our licence to operate. Compliance with chemical product regulations include product registrations, product authorisations, safety data sheets and product labels. There are also industry specific regulations that Elkem complies with, for example regulations on products that are in contact with food and water (packaging) or healthcare (band aid/wound care).
In addition to complying with chemical production regulations, the Silicones division is a signatory to the Responsible Care Global Charter of the International Council of Chemical Associations (ICCA). Product stewardship is a key pillar of the Responsible Care® programme, and by participating we are committed to manage chemicals safely throughout product life cycles. This includes both proactively identifying and managing chemical risks and concerns throughout our operations and replacing substances in the portfolio that pose unacceptable risk to human health, safety and environment.
With a portfolio of more than 4,000 different products that are used in a multitude of applications, regulatory and product compliance is key for silicones. The document management system OSCAR has been implemented and ensures that compliance, certificates and regulatory statements are easily available for distribution to customers.
Our customers have their own health, safety and environmental requirements for their products. The majority of Elkem’s safety data sheets (SDS) are available for download on www.elkem.com. The SDS for some selected products are only available on request, due to the protection of confidential business information.
Community engagement and dialogue
Input from local communities is valuable and helps us improve. Important topics that have emerged from our dialogue with local communities include community development projects, job security, safe operations, emissions and other environmental issues and traffic generated by the plant. Complaints raised by local communities and traffic incidents related to our operations are registered and managed in accordance with good practices for incident and deviation management. More information on Elkem’s procedures for handling external complaints is found in the governance and compliance chapter on page 92.
Dialogue with local communities is the responsibility of each plant or site manager and is carried out both formally and on an informal day-to-day basis. It is the plant (or site) manager’s responsibility to be aware of all relevant stakeholders and engage in dialogue where relevant, such as when changes are happening at the plant/site, and hold emergency training.
Identifying relevant stakeholders and structuring an action plan towards them is included in the certification of ISO 9001 – quality management system. In addition, we have developed our own stakeholder tool for projects and plants. The tool was piloted in 2019 and is due to be implemented in 2020.
Local community support:
A number of Elkem plants have implemented local initiatives and support programmes. Elkem’s community support includes initiatives for better education and local infrastructure, sports activities, local community poverty reduction and food support, and other social impact initiatives.
A number of Elkem plants have local initiatives and support programmes. Our local initiatives and support programmes are subject to guidelines for what is permitted and what is not, to avoid corruption. Any financial support shall be given in a fully open and transparent manner according to local legislation. It is up to the local plant or unit to set goals and to evaluate the local community programme support.
Examples of events or programmes that Elkem support locally or regionally:
- Local sports clubs, both for children and adults
- Scholarships (high school and universities)
- School programmes with focus on building technology skills
- Summer school/camps
- Cancer research programmes
- Safety training and first aid kits to local organisations
- Poor family support programmes
Elkem’s expenditures related to community support amounted to NOK 521,000 in Norway in 2019.
In 2019 we have worked on developing a universal guideline on community support for all our local engagement. The purpose of the guideline is to assist local decision makers at our plants when they engage with local stakeholders in monetary or other formal support. The support guideline is based on the principles of the UN Global Compact and, once implemented, any support shall be based on these principles. The guideline is due to be implemented in 2020.
Lobbying positions:
Elkem seeks to obtain a satisfactory regulatory framework for all its operations. In Europe, this entails a sufficient allocation of CO₂ allowances as well as compensation for CO₂ expenses in the power price. For Norway specifically, Elkem seeks a favourable outcome of the ongoing revision of the industrial grid tariff scheme, as well as to limit the number of interconnectors between Norway and other countries as this will likely increase the domestic power price. For information about lobbying activities, please visit www.elkem.com.
Responsible sourcing and the supply chain
RESPONSIBLE SOURCING AND THE SUPPLY CHAIN
Elkem sources raw materials, capital goods and services for our operations around the world. Elkem’s total procurement spend is approximately NOK 16 billion, covering supplies of raw materials, materials, energy, goods, services and logistics. The active supply base consists of about 15,000 suppliers globally.
Responsible sourcing is a strategic priority for Elkem. Responsible sourcing means looking at what we procure beyond the more traditional aspects such as cost, quality and delivery time. It means that Elkem is committed to consider ethics, labour rights, social and environmental issues when sourcing products and services across all procurement categories and across all operations.
Procurement in Elkem:
Corporate supply chain has the overall global responsibility for developing and maintaining Elkem’s procurement and logistics strategy, as well as Elkem’s global procurement policies and procedures.
Elkem’s procurement organisation is decentralised, with procurement functions both at corporate level, at divisional and plant level. We further differentiate between procurement of raw materials, and procurement of indirect materials. Suppliers of raw materials are always considered critical suppliers, and suppliers of indirect materials may be considered critical, depending on several factors.
Supplier due diligence and screening against environmental and social criteria:
The procurement function is responsible for carrying out pre-qualification and risk assessments of suppliers based on corporate requirements within environment, health and safety, social responsibility, anti-corruption and compliance with laws and regulations.
Where the risk is identified as high, additional due diligence (integrity due diligence) or on-site audits are required.
In 2019, 73% (ex. China) of new suppliers of raw material were screened against environmental and social criteria. For high risk suppliers, additional due diligence was conducted (integrity due diligence). One supplier was excluded based on due diligence findings.
In 2020/2021, Elkem is updating its supplier due diligence process, aiming for a harmonised approach to screening using social criteria. All new suppliers will be screened against the topics in the GRI 400 series.
SUPPLIER AUDITS
The number of raw material suppliers is relatively low. A structured auditing program is in place to ensure all suppliers receive regular audits.
For suppliers of goods and services such as hardware, plant equipment and services, the number of suppliers is high. Regular audits are performed by plant personnel or corporate personnel, focusing on supplies that are associated with risk.
Relevant Elkem policies on responsible sourcing are:
- EHS and CSR approval of Elkem’s suppliers and business partners: Outlines Elkem’s procedure for pre-qualification and management of suppliers.
- Corporate standard for sourcing bio-carbon: Outlines Elkem’s commitment to sustainable forest management and the requirements for procuring bio-based reductants in Elkem.
Code of conduct for Elkem’s business partners:
In October 2019, Elkem launched the code of conduct for Elkem’s business partners (“the business partner code”). The business partner code sets out Elkem’s expectations of our suppliers with regards to ethics, labour rights and social and environmental issues.
We require all new suppliers to endorse the business partner code and maintain their commitment throughout the relationship. The business partner code is considered an integral part of any agreement that regulates the relationship between Elkem and a supplier.
EHS in the supply chain
Elkem has developed detailed requirements for high risk suppliers and contractors regarding health, safety and environmental standards for operations like mining, transportation, storage and loading, and is actively involved in the promotion and monitoring of safe and decent working conditions. This includes health and safety training and providing correct personal protection equipment for suppliers’ employees when necessary. Age control to prevent child labour and ensure responsible working conditions for young employees is also carried out. Elkem requires suppliers and contractors to engage their employees with written contracts on fair terms, and to give them information about their right to organise and collectively bargain with management where this is legally possible.
Elkem’s requirements are regularly discussed in meetings with suppliers. High-risk suppliers must document their understanding of legal requirements and hazards in their operations and present plans showing how risk will be eliminated or controlled while working for Elkem. Elkem performs audits and inspections, both in connection with routine visits for quality, technical and business follow-up, and as unannounced site visits. External auditors also conduct supplier audits on Elkem’s behalf.
Violations of Elkem’s requirements are registered and addressed with verbal or written warnings in addition to requests for improvements when necessary. Repeated violations may lead to requirements for speedy implementation of improvement plans, financial penalties, or termination of contracts with immediate effect.
Strategic partnership with Achilles:
In 2018, Elkem entered into partnership with supply chain risk management solution Achilles. A large portion of our Norwegian and Islandic suppliers are pre-qualified through this solution. Achilles also performs 10,000 audits per year.
Continuous improvement:
As one of the world’s leading suppliers of silicon-based advanced materials with operations throughout the value chain from quartz to specialty silicones, we are continually improving the way we source our supplies. As Elkem is growing into new emerging markets, we recognise the need to optimise, streamline and digitalise our supply chain management and run projects to improve our capabilities to this end.
New harmonised process for supplier management:
In 2020/2021, Elkem will implement a global supplier management system and introduce a new harmonized process for supplier prequalification, supply chain management, supply chain risk management and contract management.
This will allow for a unified process for screening and vetting suppliers across all divisions and jurisdictions, tracking and monitoring suppliers’ compliance throughout the contract lifecycle, as well as identifying and managing supplier risk.v
Human rights
Elkem’s operations cover challenging markets such as China, Malaysia, Korea, India, South Africa, Russia, Brazil, Mexico and Paraguay. Human rights issues are often deeply embedded in the local culture and can only be mitigated by engaging with stakeholders, governments and local communities.
Elkem is committed to the UN Guiding Principles on Business and Human Rights. We also respect and follow the requirements of the UK Modern Slavery Act and the French Duty of Vigilance Law.
Compliance with these principles require Elkem to identify and assess the human rights risks and impact of our operations and our supply chain.
Relevant Elkem policies on human rights include:
- Elkem Code of Conduct: Expresses our respect for human and labour rights.
- Elkem Code of Conduct for Business Partners: Requires our suppliers to commit to global human rights principles.
- Policy for Corporate Social Responsibility: Describes how Elkem and the Social Corporate Responsibility (CSR) Committee is working to protect human rights and protect workers’ rights.
Human rights impact assessment (HRIA):
Our policies on human rights express our commitment to human rights and how we work to protect human rights in Elkem and in the supply chain. Human rights, and especially workers’ rights, have always been a top priority for Elkem, and an integral part of our EHS audits. More information on our policies regarding child and forced labor can be found in the attractive employer chapter on page 72.
As we grow and enter into new and challenging markets, we see the need to take on a more systematic approach to our human rights strategy. We have therefore initiated a Human Rights Impact Assessment (HRIA), where we work to identify Elkem’s actual impact and the risk of impact on human rights throughout our value chain.
Elkem recognises that human rights impact is constantly evolving. We are therefore committed to update our impact assessment on a regular basis, or whenever external factors or Elkem’s operations require it, for instance where we enter new markets, develop new products or acquire new business entities.
Human rights priorities:
Based on the HRIA, we will identify Elkem’s human rights priorities and launch a human rights action plan. In 2020, we are also launching a human rights training programme and developing a compliance monitoring programme on human rights.
Grievance mechanisms:
In accordance with the UN Guiding Principles on Business and Human Rights, Elkem is committed to remedy situations where Elkem’s activities have caused or contributed to adverse human rights impacts. If something is not right, Elkem wants to know about it. That is why we have set up an external Speak up channel that allows for anonymous reporting and engaging with stakeholders. The Speak up channel is available to external stakeholders through the Elkem webpage.
How we respond to adverse events:
Even with the best practices, a business may cause or contribute to an unforeseen adverse human rights impact that was not foreseen or which it was unable to prevent. In such events, Elkem will do its outmost to prevent or mitigate the impact:
- Where Elkem causes an adverse human rightsimpact, we take the necessary steps to cease or prevent the impact.
- Where Elkem contributes to an adverse human rights impact, we take the necessary steps to cease or prevent our contribution and use our leverage to remediate any impact to the extent possible. Whenever we have leverage to prevent or mitigate the adverse impact, we exercise it.
- Where we have no leverage, we terminate the relationship.
When necessary, we consult externally with credible, independent experts, including governments, civil society, national human rights institutions and relevant multi-stakeholder initiatives
Governance and compliance
Targets
Elkem considers good corporate governance to be a prerequisite for value creation, trustworthiness and for access to capital. In order to secure strong and sustainable corporate governance, Elkem strives for good and healthy business practices, reliable financial reporting and an environment of compliance with legislation and regulations across the group.
Corporate governance and compliance
CORPORATE GOVERNANCE
Elkem’s framework for corporate governance is outlined in Elkem’s corporate governance policy, which covers the instructions for the audit committee, the instructions for the nomination committee, the instruction for the remuneration committee, rules for primary insiders and instructions for handling inside information. The document is reviewed annually by the board of directors and was last amended on 21 October 2019.
Elkem endorses the Norwegian Code of Practice for Corporate Governance (“NUES” or the “Code”). The principles of the Code are reflected in the corporate governance policy and in all other governance documents.
Governance documents:
- Articles of association
- Corporate governance policy
- Policy for corporate social responsibility
- Global code of conduct
- Code of conduct for Elkem’s business partners
- Speak up policy
- Anti-bribery and corruption policy
- Competition law compliance policy
Risk management and internal control:
It is ultimately the responsibility of the board of directors to ensure that Elkem has sound and appropriate internal control systems and risk management. To that end, the board of directors conducts an annual review of the company’s most important areas of exposure to risk and such areas’ internal control arrangements.
Operative management has ownership, responsibility and accountability for directly assessing, controlling and mitigating risk and assuring adequate internal controls. Management provides frequent and relevant reporting of both operational and financial matters to the board of directors, ensuring that the board has adequate information for decision-making and can respond quickly to changing conditions.
Corporate help chains, such as EHS, quality, product stewardship, compliance, Corporate Social Responsibility (CSR), legal, IT, finance and other control departments, oversee, facilitate and report on the risk management activities of operative management.
Due to Elkem’s size and risk exposure in China, Elkem has recently (2019), set up an Internal audit and compliance function for Asia. The function reports to VP finance and accounting.
Audit Committee:
The audit committee is a sub-committee of the board of directors and its objective is to act as a preparatory body in connection with the board’s supervisory roles with respect to financial reporting and the effectiveness of the company’s internal control system.
The CFO reports on Elkem’s internal control and compliance work to the audit committee of the board upon request, in cooperation with VP finance and accounting, and General Counsel.
For more information on Elkem’s internal control and risk management systems, please see the board of directors report and information on the investor relation pages on www.elkem.com.
COMPLIANCE
In 2019, Elkem engaged a corporate compliance officer to lead the company’s compliance programme. The corporate compliance officer reports to general counsel.
Corporate compliance is further supported by the newly appointed internal audit and compliance function in China on compliance and human rights issues.
Network of compliance champions set up in 2019:
Corporate compliance is supported by a network of compliance champions across Elkem’s operations. The compliance champions are members of management or support functions, stationed in each business unit, that assist the corporate compliance function in implementing Elkem’s compliance programme, including training and guidance to their respective units.
Corporate Social Responsibility Committee:
Elkem has a CSR committee, which is headed by Senior Vice President (SVP) HR with participants from key functions such as compliance, legal, EHS, communications, HR, procurement and sales. The committee meets on a regular basis and is tasked with promoting a culture that emphasises and sets high standards for corporate social responsibility, as well as review of corporate performance against those standards. SVP HR is responsible for reporting CSR issues to the CEO and for reporting major issues to the board of directors.
Compliance programme audit in 2020:
Elkem is committed to continuous improvement. As a measure to improve, Elkem will engage external consultants to conduct an independent assessment of the compliance programme in 2020.
Speak up channel
At Elkem, openness is key, and employees and stakeholders are encouraged to speak up if something is not right. Employees should feel free to discuss issues with management, or report misconduct to HR or the legal/compliance department without risk of facing consequences.
Global tool for external misconduct reporting:
In 2019, Elkem rolled out an external Speak up channel for misconduct reporting and updated the company’s Speak up policy. The Speak up channel is available to all employees and allows for anonymous reporting in all Elkem languages. The policy gives clear guidance on how to report a concern.
The Speak Up channel and the Speak up policy are available and communicated through our intranet site, the Elkem webpage, through training and physical posters and handouts at plants and offices.
This channel also functions as a grievance mechanism for external stakeholders, such as suppliers, costumers, local communities where Elkem operates. The Speak up channel is available on the Elkem webpage and grievances can be reported in the several languages.
Handling of misconduct reports:
Misconduct reports are handled by corporate compliance and in accordance with applicable legislation on misconduct reporting. Elkem has a zero tolerance for retaliation against those who report a concern and will sanction those who retaliate.
Training
Global online training programme:
Elkem is committed to providing up-to-date, relevant and engaging compliance training. In 2020 Elkem will roll out a new global online training programme with relevant e-learning to all employees, including training in ethics, anti-bribery and corruption, and anti-competitive practices. The training is refreshed on a regular basis, providing employees with new and updated content each year. Employees can choose to complete the training in all key Elkem languages.
Risk based face-to-face trainings:
The online training is supplemented by face-to-face trainings in high risk jurisdictions and for high risk employee groups. The trainings are tailored to the specific risks and needs of the target group.
Anti-competitive practices, anti-bribery and corruption
ANTI-COMPETITIVE PRACTICES
Elkem is committed to avoiding anti-competitive practices across all operations. The competition law compliance policy outlines what behaviour is considered acceptable or not.
To improve preventive measures a full overview of operations and employee groups that are most exposed and to what anti-competitive practices needs to be updated. We are therefore conducting an anti-competitive practice risk assessment to identify high risk jurisdictions and employee groups, as well as identifying red flags and mitigate gaps. The assessment is due in 2020.
ANTI-BRIBERY AND CORRUPTION
Elkem has a zero-tolerance policy against corruption. Elkem has multiple operations across jurisdictions and in several high-risk countries. Elkem also deals with government officials for permits and other administrative issues.
In order to enhance the efficiency of Elkem’s internal controls and measures to prevent bribery and corruption, compliance is conducting an anti-bribery and risk assessment (ABC risk assessment) of the company’s global operations. The assessment is due 2020 and will form the basis for the anti-bribery and corruption programme going forward. The 2020 assessment will be updated on a regular basis and upon entering new markets and introducing new products.
Working with business partners
It is important to Elkem to work with business partners of high ethical integrity. Elkem does not accept bribery, environmental breaches, or human rights violations on behalf of our business partners. Relation managers are required to carry out the adequate due diligence on business partners before entering the business relationship. In Norway and Island, suppliers are required to prequalify through Achilles.
Code of conduct for business partners:
In 2019, Elkem rolled out a new code of conduct for business partners, which builds on the global code of conduct, anti-corruption policy, CSR policy and human rights policy. All new suppliers are required to commit to and sign the code to become business partners of Elkem.
Third-party risk management system:
Bribery cases, human rights breaches, environmental disasters and EHS scandals routinely involve business partners, such as agents, consultants, suppliers, joint venture partners and distributors. In order to ensure that we handle the risk associated with such business partners in an efficient way, Elkem is rolling out a Third-party Risk Management System (TPRM). The system will allow for risk assessment of all business parties, screening against sanction lists and adverse media, as well as risk based due diligence, audits and monitoring of business partners throughout their lifecycle. The system is due to be implemented in 2020/2021.