- Elkem
- About Elkem
- Elkem Business System
Elkem Business System – our culture and our way of working
Elkem Business System (EBS) plays an important role in all Elkem's business. EBS is first and foremost about empowering the people value chain to deliver excellence, identify problems and improve the business in these four dimensions; HSE, Value, Quality and Time.
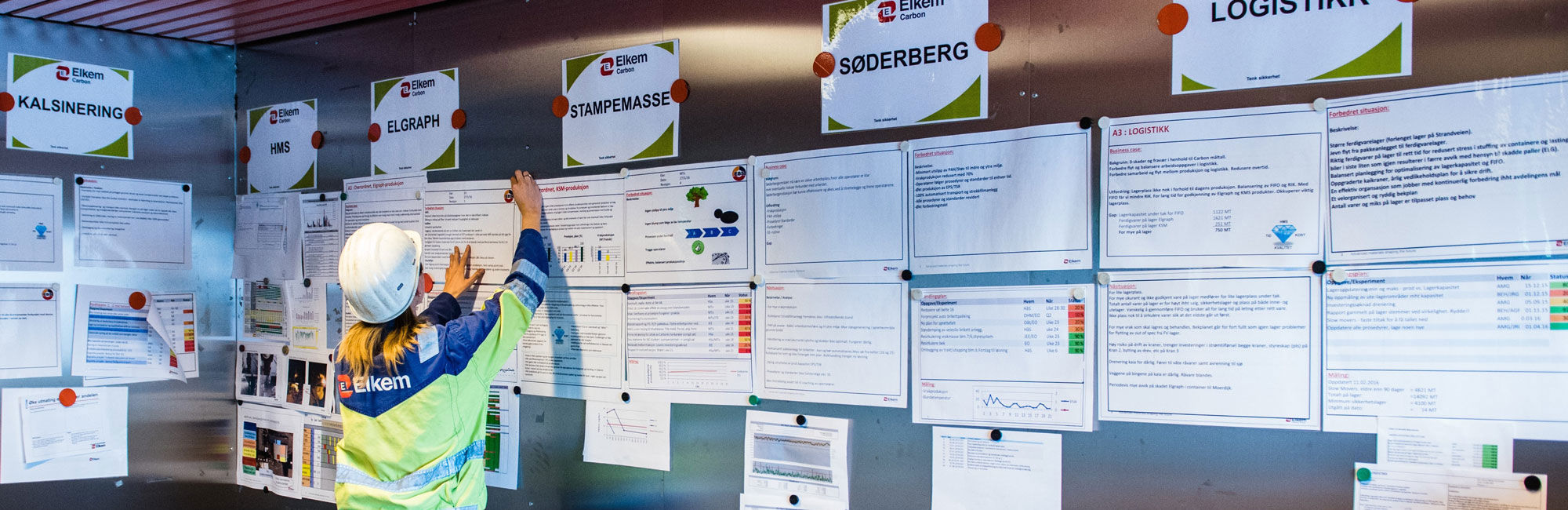
EBS is supporting the strategic direction and goals of Elkem and drives the behavior in the organization towards a culture of excellence, continuous improvement and deep learning.
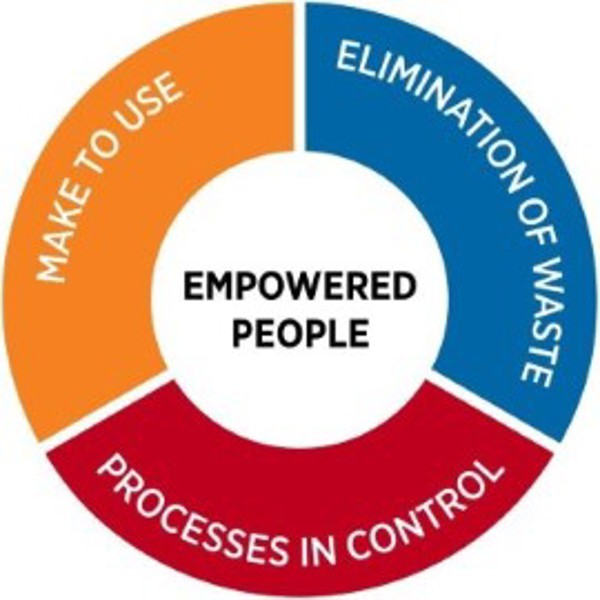
EBS is founded on four basic principles:
1. Empowered people
People linchpin the system, is a conviction that each and every success is attributable to at least 70% human effort and just 30% to the system behind it. The people doing the work are the experts and the driving forces for excellence and improvements of our business and value chains.
2. Make to use
Demand driven production, make what the customer wants when the customer wants it and the correct Quality and Quantity. Puts the customer, both internal and external, in focus. The principle states that everyone in the organization – down to the individual level – is connected as internal customers and suppliers in close relation to each other.
3. Eliminate waste
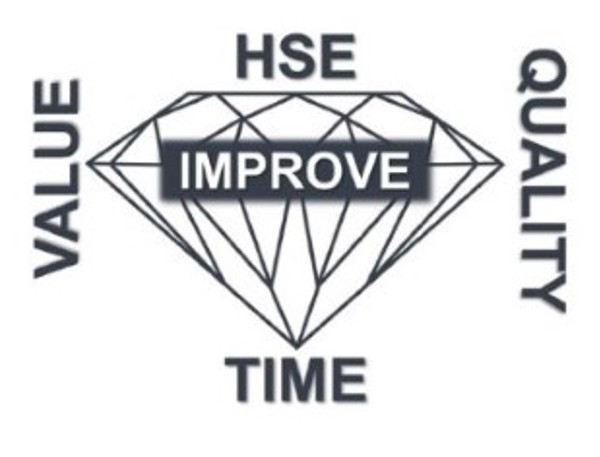
Represents our continuous strive for perfection and that everyone in Elkem participates to continuously simplify and improve the processes by eliminating waste (Muda, Mura and Muri). It concerns people’s participation in simplifying, improving and finding new solutions.
4. Processes in control
Predictable and stable processes provides results that satisfy the customer. This principle puts focus to the processes where we strive for removing unwanted variations.
Contact us
Take your business to the next level by partnering with a world-leading material manufacturer.