- Elkem
- Digital communication
- Smartphones, 5G, computers & wearables
- Potting electronics
Potting and sealing electronics with silicone
Make your electronics last longer and give better performance with silicone potting and encapsulation
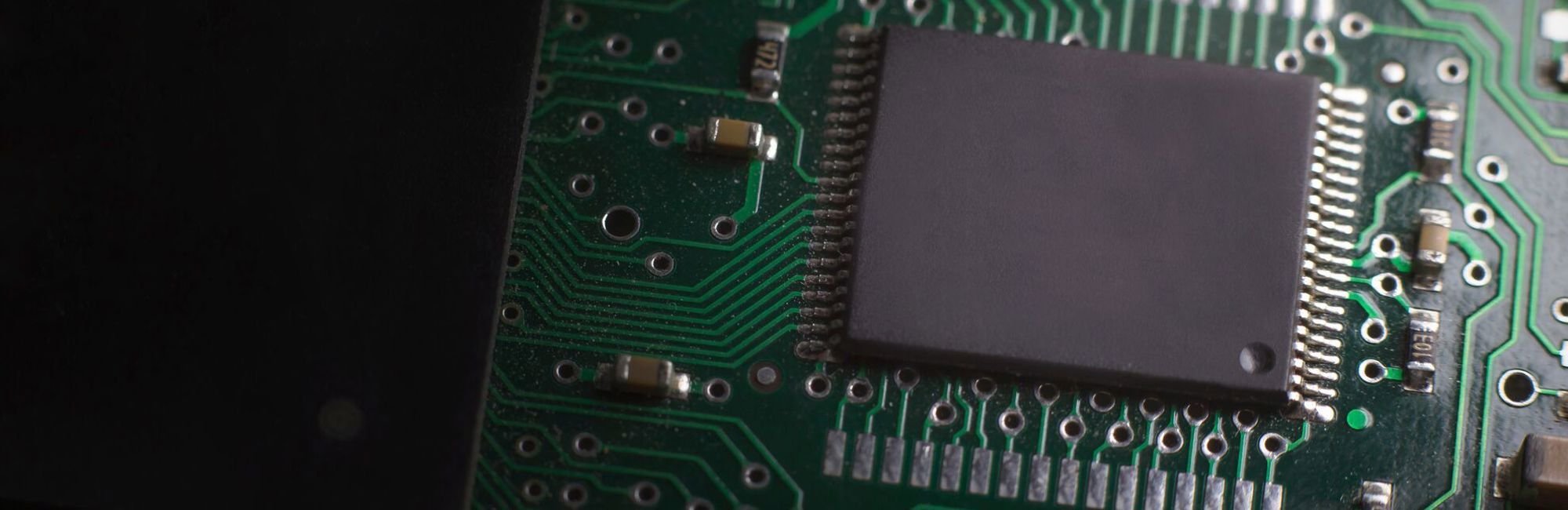
How silicones can help protect and ruggedize electronics?
Silicone potting and sealing of electronics is a process of encapsulating electronic components in a protective coating. This process is used to protect components from dust, moisture, vibration, and other environmental factors that could compromise the integrity of the product. The process also offers EMI/RFI shielding, and improved product aesthetics.
The silicone used in the process is typically a two-part system of an A component and a B component that, when mixed, create a fully cured silicone coating. The silicone coating is applied to the components either manually or by automated dispensing systems, and then cured at an elevated temperature. The resulting silicone-encapsulated product is highly reliable and resistant to environmental and vibration-induced damages.
Elkem Silicones offers a broad range of silicone rubbers and gels within the range of CAF™ RTV-1 and BLUESIL™ ESA RTV-2, which are recommended in electronic applications to ensure mechanical and environmental protection.
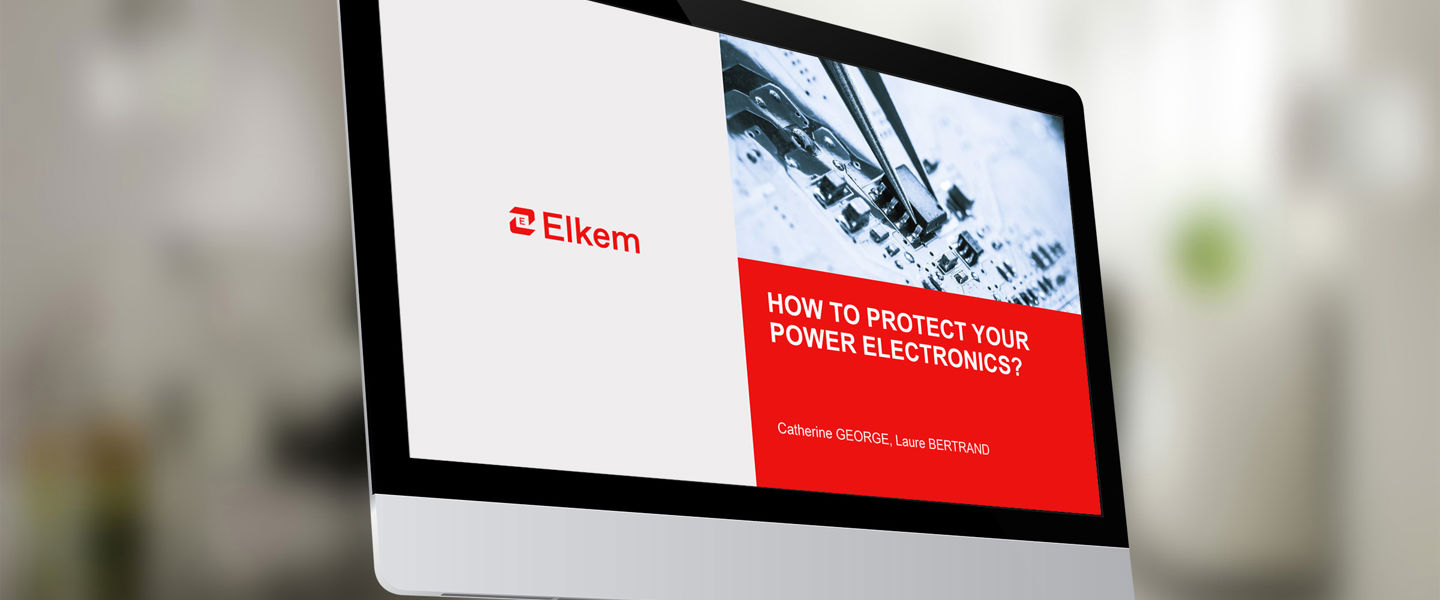
Webinar : How to protect your power electronics?
A half-hour deep dive into materials science, protective technologies and sustainable product selection for electronics engineers.
The wide acceptance of silicones in the electronics industry is due to several technical and mechanical properties including:
- Mechanical strength
- Dielectric strength
- Moisture resistance
- Low modulus to protect internal stress
- Damping properties
- Environmental resistance
- Excellent adhesion if needed
- Flame resistance, UL 94 flammability
- Optical clarity or thermal resistance over a wide range of temperatures.
Silicones, because they are stable, ensure that your electronics components are safe in terms of electrical insulation, adhesion, temperature and fire resistance. They are durable and reliable materials, extending your electronic components’ lifecycle, allowing devices to last longer and eventually reducing landfill waste.
The main applications where silicones are the best candidate to protect your electronic components include:
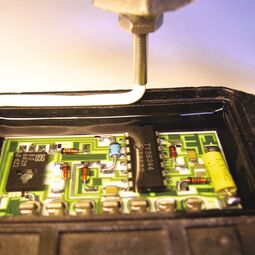
- Potting electronics using BLUESIL™ RTV-2 (room-temperature vulcanizing) gels and paste for solar modules, junction boxes, power electronics, IGBTs, sensors, CPUs, etc.
- Optically clear potting provides high transparency in the UV-visible wavelength associated with outstanding optical stability, making BLUESIL™ ESA 7250 A&B and ESA 7255 A&B series an excellent candidate for encapsulation of a variety of LED device designs.
- Encapsulation with CAF™ RTV-1 and BLUESIL™ RTV-2 products for various components on PCBs.
Elkem supplies tailor-made, low-volatile, low-viscosity silicone gels to meet your specific requirements for high thermal conductivity, electrical conductivity or sensitive electronic applications. Thanks to our global presence and supply-chain services – as well as our design and process experts available worldwide – you can benefit from the outstanding technical support you need to help you find the silicone potting and encapsulation solutions that meet the needs of you and the end user.
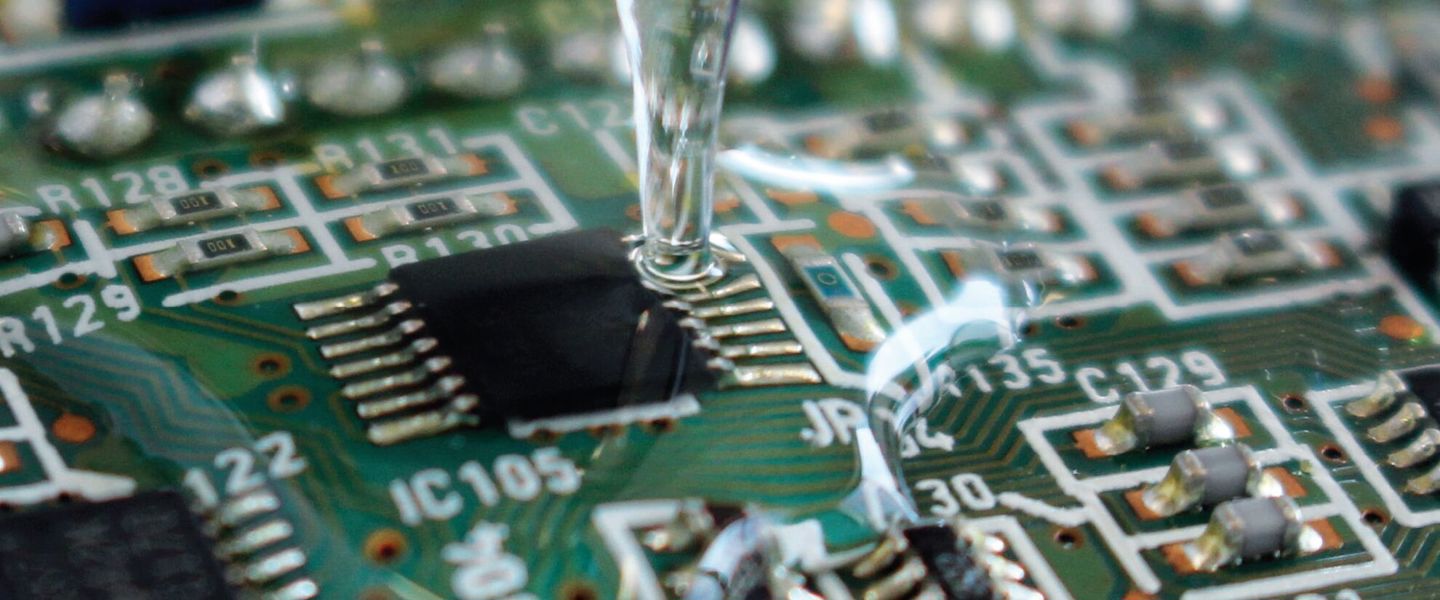
The 8 benefits you need to know to protect electronics using encapsulation and potting
A primarily addressed article to electrical and electronics engineers in all industries who are involved in designing, producing and protecting critical electrical and electronic components
Contact us
Take your business to the next level by partnering with a world-leading material manufacturer.