- Elkem
- Energy & power
- Oil & gas
- Oil well cementing
Elkem specialty and microsilica products for oilwell cementing
Our portfolio of specialty oilfield cement additives achieve the desirable combination of high performance, reliability and cost-effectiveness, while also being environmentally safe.
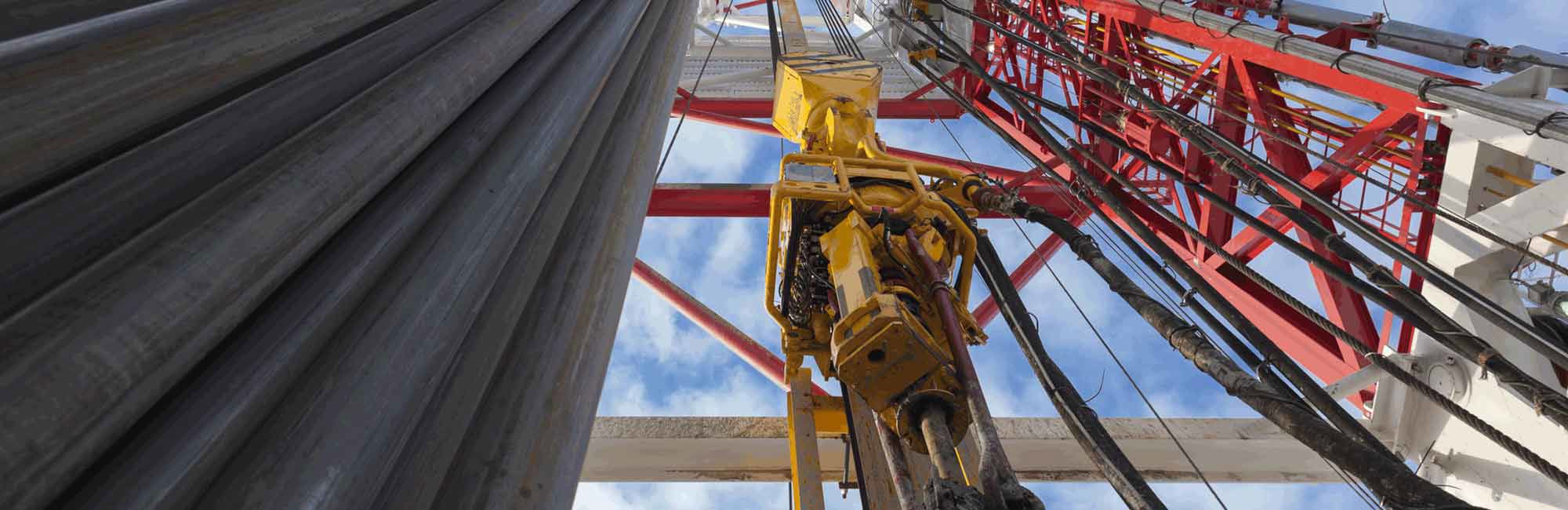
Elkem oilfield cementing materials: improved well integrity
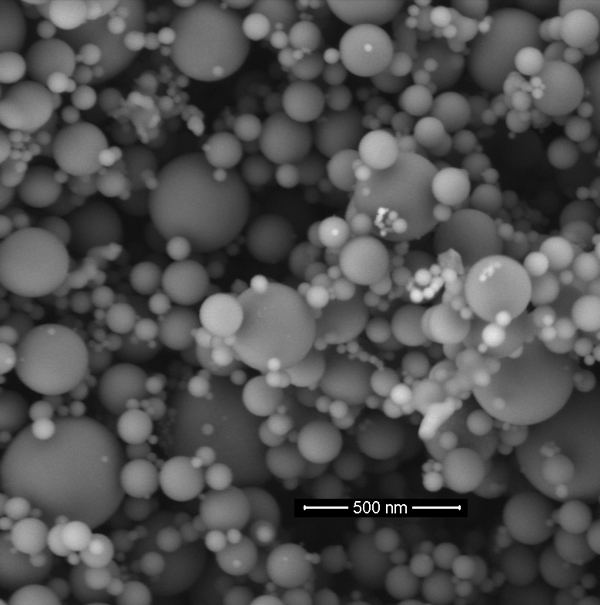
Oilfield cementing involves the placement of a solid and impermeable setting material that supports and isolates the different well zones, ensuring well-integrity. Petroleum operators and their service providers use a wide array of cementing chemical additives to ensure safe and reliable cement placement across the wellbore and long-term zonal isolation. Cement must also provide support for casing/liner strings and resist deformation of surrounding areas protecting metal tubulars from corrosive gases and brines, thus preventing future collapse. During cement placement in the well, special fluids such as spacers are used to prevent downhole contamination. Cement slurries may also require accelerator or retarder additives to control the pumpability of cement, known as thickening time. Extenders or weighting agents are added to the cement blend to tailor the density of the job in each well. Other oilfield chemicals, such as dispersants, high-performance fluid loss additives or anti-gas migration prevention products or defoamers can also be added to tune the rheological slurry properties of the cement and control the fluid-loss against the potentially permeable rock formation. A properly designed cement slurry and cement operation is key to the lifespan of the well and its performance over time, complying with safety and environmental standards.
Ensuring results in oilfield cementing operations
The Elkem portfolio includes a comprehensive range of high-performance, reliable, cost-effective and environmentally safe – often PLONOR listed – specialty oilfield cement additives. This includes extenders, defoamers, fluid-loss control, gas-migration and proprietary weighting agents, as well as Microsilica-based additives to ensure that cement or resins bond to the casings and formations and provide adequate mechanical properties.
See below for an overview of our portfolio.
Oilfield related pages
Contact us
Take your business to the next level by partnering with a world-leading material manufacturer.