- Elkem
- Sustainability
- Elkem’s environmental and energy strategy
Elkem’s environmental and energy strategy
Elkem works continuously to reduce the company’s environmental footprint. Elkem’s sustainability philosophy is based on the general principle of producing as efficiently as possible and with the maximum use of all input streams, like materials and energy.
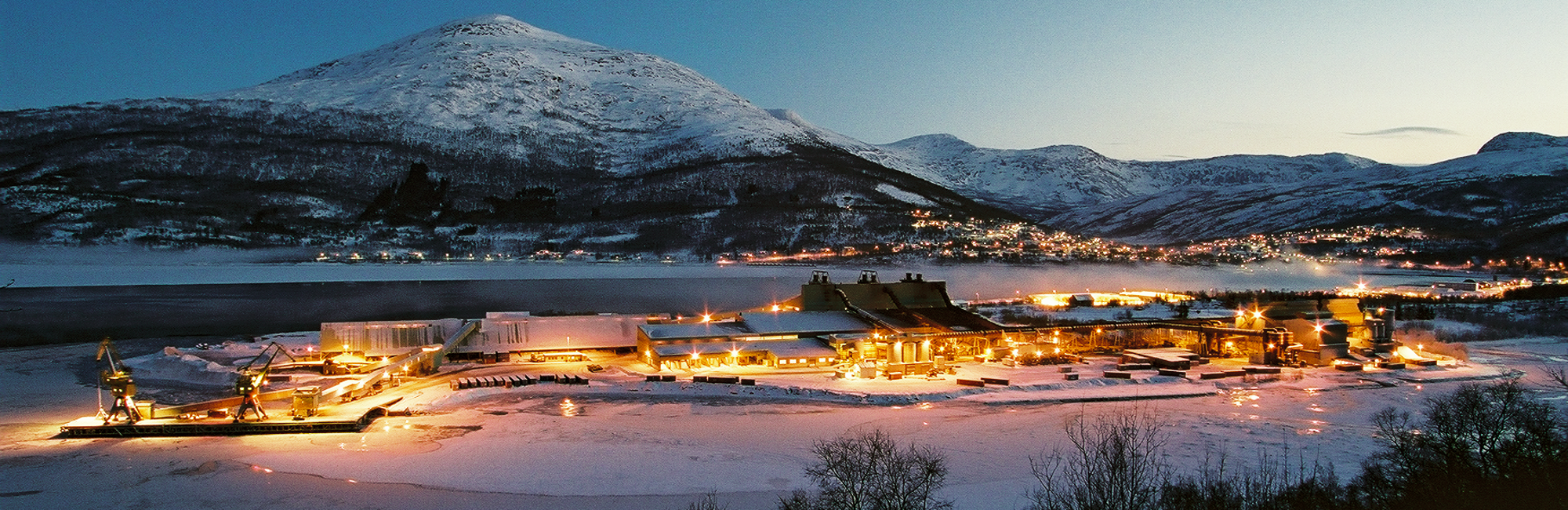
All divisions and plants are responsible for implementing environmental and energy strategies, and conducting their business in accordance with Elkem’s principles in this area. Well established group-wide audit and reporting systems for EHS are also being expanded to include a higher level of focus on environmental and energy issues.
As Elkem continues to grow in new segments of the silicone value chain, strategic targets in this area include:
- Mapping and understanding Elkem’s total environmental impact.
- Expanding Elkem’s worldwide EHS reporting regime to include better environmental and energy indicators.
- Greater understanding of critical emissions and discharges (i.e. COD, dust, CO₂, SO₂, NOX, PAH), and setting ambitious targets for reduced emissions
- Minimising the use of landfills and striving to avoid waste through efficient processes and/or recycling into valuable products
- Implementing energy management systems at all sites that have not already done this by end of 2018
- Setting ambitious targets for energy consumption and energy recovery at all sites worldwide
Carbon neutral metal production
Elkem is among the world’s cleanest metal manufacturers, but our silicon and ferrosilicon production process are big emitters of CO₂. Elkem seeks to reduce fossil CO₂ emissions by replacing fossil coal with biocarbon as a reduction agent in our smelting furnaces. Elkem has a pronounced goal of using 20 per cent biocarbon in the mix of reduction materials in the production of silicon and ferrosilicon alloys in Norway within 2021 and 40 per cent within 2030.
Energy efficiency
Elkem is constantly seeking ways to reduce energy consumption per produced unit. There are three ways to reach this goal: Increasing the production yield, recovering heat from the furnace off gases and carefully managing other energy consumption.
Silicon alloy production is energy intensive. In addition to electricity, the production process requires adding carbon-based reduction materials in vast quantities to the process that also represent a large amount of energy.
The most effective method to reduce the energy used per produced tonne of ferrosilicon or silicon is to make the production process more energy efficient. Elkem has some of the most energy efficient smelting furnaces in the world, but still see a potential for improvements. A dedicated research and development project called Si2020 focuses on furnace design, process control, refining, and optimal use of raw materials.
Energy recovery
There are two main methods to recover energy from the smelting process. Both have their advantages and challenges. The first method recovers energy by utilising surplus heat directly in the form of steam or hot water. This is very efficient, but not very feasible, as most of Elkem’s plants are located in sparsely populated areas where there is little demand for heat neither from local communities nor other industry.
In the second method for energy recovery, surplus heat is used to produce electricity. The advantage is that electricity can be fed into the power grid. The downside is that two thirds of the energy is lost in the transformation.
Elkem currently uses both methods. In Norway, Elkem Thamshavn currently generates around 160 GWh of electricity every year, and Elkem Bjølvefossen has increased its generating capacity from 40 to 80 GWh per year, after the recovery facility upgrade was finished in March 2016. At Elkem Carbon in China approximately 35 GWh electricity is recovered annually, and at Elkem Salten, Norway, the new energy recovery plant is expected to be finished later this year.
Maintaining an intense focus on energy efficiency has made Elkem Thamshavn, Norway and Elkem Chicoutimi, Canada the world’s most energy efficient smelting plants for silicon and ferrosilicon production respectively.
Energy management
Several Elkem sites are certified to ISO 50001 and a number of sites have implemented an energy management system which is aligned with the requirements of ISO 50001. Additionally, a number of sites have implemented energy management systems, but not necessarily in line with ISO 50001 requirements.
The process has showed that even small measures, such as better insulation, motor inspections, lighting management, sealing leaks in compressed air systems and heating and cooling control, can produce substantial savings, even though each individual measure is relatively small compared with the energy consumption of a smelting furnace. Potential energy savings of 10% of auxiliary energy have been identified.
Contact us
Take your business to the next level by partnering with a world-leading material manufacturer.