- Elkem
- Mobility & transportation
- Parts manufacturing
- Ductile iron
Foundry alloys for ductile iron
Controlling spheroidal graphite formation with foundry alloys
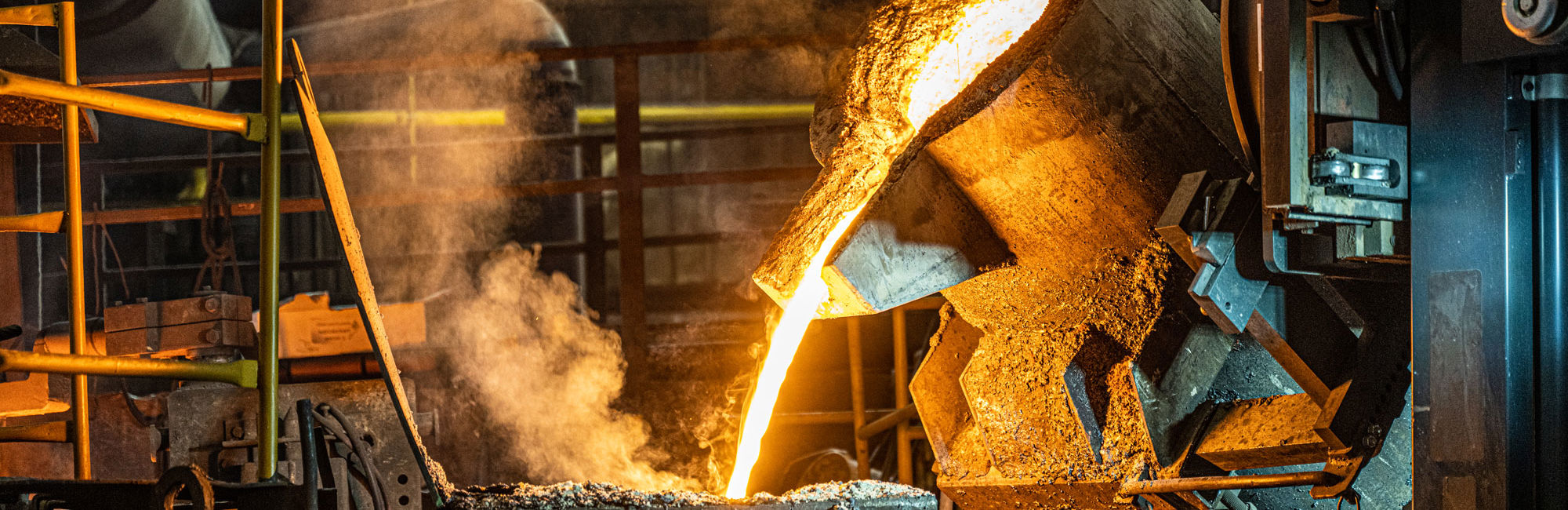
Ductile iron is a versatile material that has grown in popularity over recent decades, due to its excellent mechanical properties and castability. For these reasons, ductile iron castings are the preferred choice in many sectors, including wind energy, engineering and automotive industries. At Elkem we provide an unbeatable combination of quality products and expert advice on ductile iron manufacture – in whatever country you’re operating.
Ductile iron: Improving casting product quality and production efficiency
Ductile iron, also known as spheroidal graphite iron (SG iron) or nodular cast iron, contains carbon in the form of spherical graphite nodules. These prevent crack propagation, and give a material that has a higher tensile strength, impact resistance and fatigue resistance compared to gray iron.
The matrix of regular ductile iron is usually ferritic and/or pearlitic, but in austempered ductile iron (ADI) the matrix is transformed into ausferrite by a carefully controlled heat treatment process, giving an iron with even higher strength than regular ductile iron.
At Elkem, we offer a wide variety of precisely-formulated foundry alloys to ensure defect-free casting of ductile iron and ADI products, while also streamlining production and making it more economical. These can be divided into recarburizers, preconditioners, conditioners, nodularizers, inoculants and inserts.
Recarburizers for ductile iron
High-purity recarburizers are particularly useful for adjusting carbon levels in ductile iron base metal during charging of the furnace, and as a ‘trimming’ addition just before tapping from the furnace. Use of highly crystalline recarburizers ensures easy dissolution and maximizes carbon recovery.
Preconditioners for ductile iron
The addition of preconditioners to ductile iron melts can help to enhance and stabilize the nucleation potential of the base iron, avoiding later nucleation ‘fade’ and resulting in better-quality castings.
Conditioners for ductile iron
The introduction of magnesium ferrosilicon (FSM) nodularizer to molten iron in the treatment ladle generates an intense reaction, causing loss of nucleation and variable magnesium recovery. These challenges can be largely overcome by using a specially formulated conditioner (also known as a cover alloy) in sandwich and tundish ladles.
Nodularizers for ductile iron
With recarburization and preconditioning complete, the next step in the production of ductile iron is treatment of the melt with a magnesium ferrosilicon nodularizer, which initiates and controls the precipitation of graphite nodules during solidification.
The use of carefully optimized grades of nodularizer makes it easier to minimize the quantity used. In turn, this reduces production costs and energy losses, avoids splashing during tapping, reduces the formation of excessive fumes, and limits the loss of nucleation potential.
Inoculants and inserts for ductile iron
The addition of inoculants is an essential step in the treatment of ductile iron to ensure the precipitation of well-rounded uniformly-distributed nodules in a carbide-free matrix.
Inoculants can be added just before casting, or in the mold itself, in which case they are termed inserts.
The Elkem advantage
Elkem has been helping iron foundries with their alloy requirements for many decades. Over this time our attention to detail and willingness to tailor our offering have always been high on our agenda – only the best is good enough for our customers.
And with cost, quality and sustainability increasingly important for iron foundries, we’re constantly looking out for ways to improve our products and processes. Whether it’s developing new formulations or consolidating our worldwide presence, we’re always trying to enhance how we can help our customers.
MORE ABOUT FOUNDRY ALLOYS
Contact us
Take your business to the next level by partnering with a world-leading material manufacturer.